When it comes to handling long, heavy, and awkward loads in tight spaces, few companies are as trusted or as experienced as ASI Associate Member, Hubtex Australia. Now in its 30th year of operation, the company has built a solid reputation across the steel industry by delivering specialist materials handling solutions, and backing that up with a level of service support that’s hard to beat.
Founded in 1995, Hubtex Australia was established to meet a growing need in the Australian market: the safe, efficient handling of long loads.
“Right from the start, we saw the steel industry was in urgent need of better ways to manage long products,” said Bruce Peatman, Managing Director of Hubtex Australia. “Back then, sideloaders were rare. Steel was often handled with conventional forklifts or cranes. We helped introduce more efficient equipment to the sector and worked with our customers to reshape their entire approach to long load handling.”
Today, Hubtex Australia is the country’s leading supplier of multidirectional sideloaders and forklifts, representing world-class brands including HUBTEX, Genkinger, Bulmor, Bendi, Drexel, Systraplan, and Hoppecke. Their solutions are tailored to suit the needs of steel stockholders and processors, with an emphasis on safety, reliability, and efficiency.
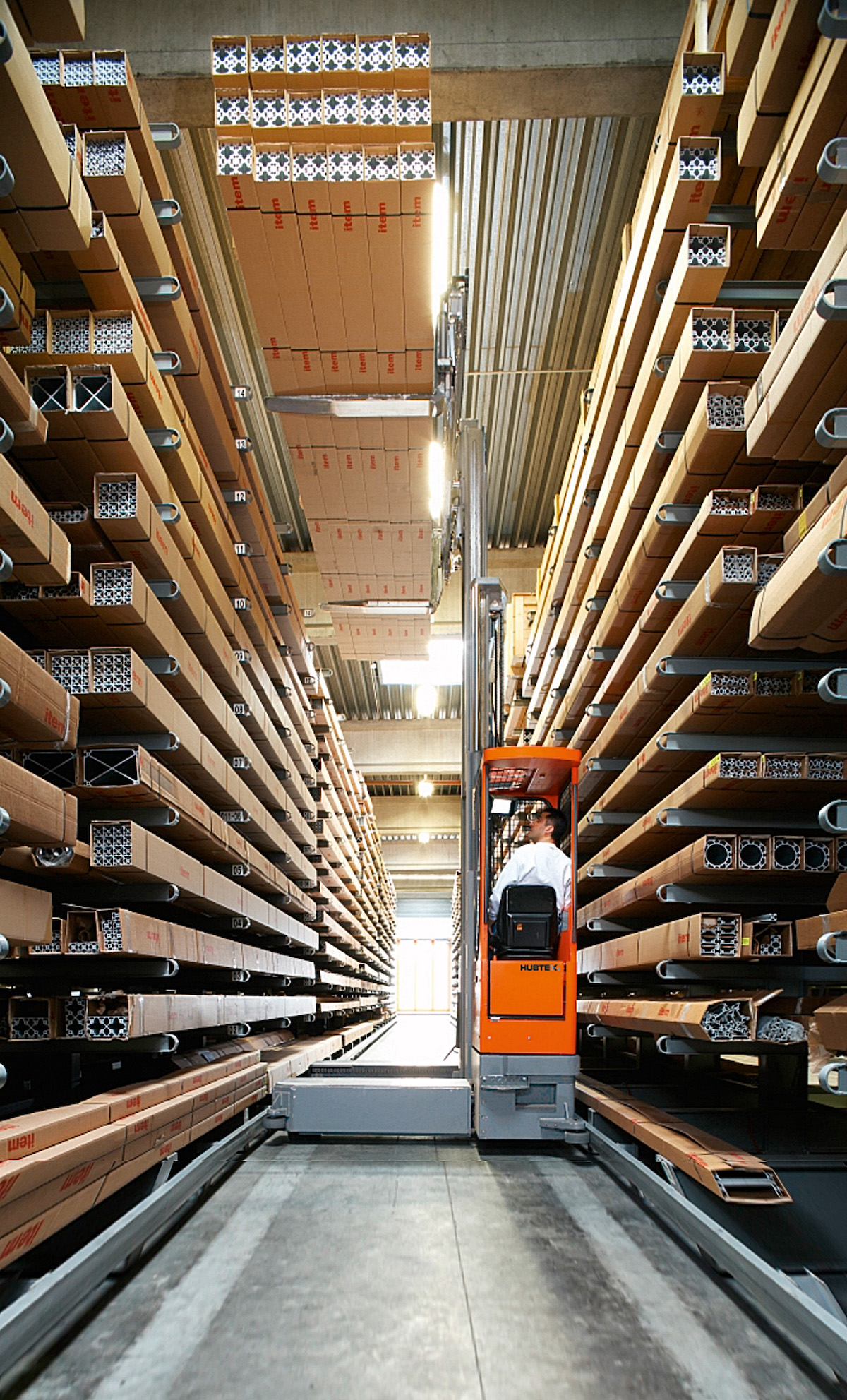
Purpose-Built for the Industry
Hubtex Australia’s core business is built around German-engineered equipment that’s specifically designed to move heavy, awkward materials through narrow aisles. This includes everything from long steel sections and tubing to coils and other bulky products.
“We’ve spent the last three decades working alongside steel companies to deliver solutions that suit their exact needs,” said Peatman. “It’s about improving safety, reducing product damage, and increasing throughput—all while making better use of warehouse space.”
Hubtex’s solutions are available new, refurbished, or on rental terms, and include high-performance forklifts that can manoeuvre in aisles as narrow as 1.5 metres. Their range includes both battery-electric and lithium-ion powered machines that help steel businesses reduce their environmental footprint.
But the true game-changer is the company’s latest release: the FluX 30 Multi Directional Forklift Truck.
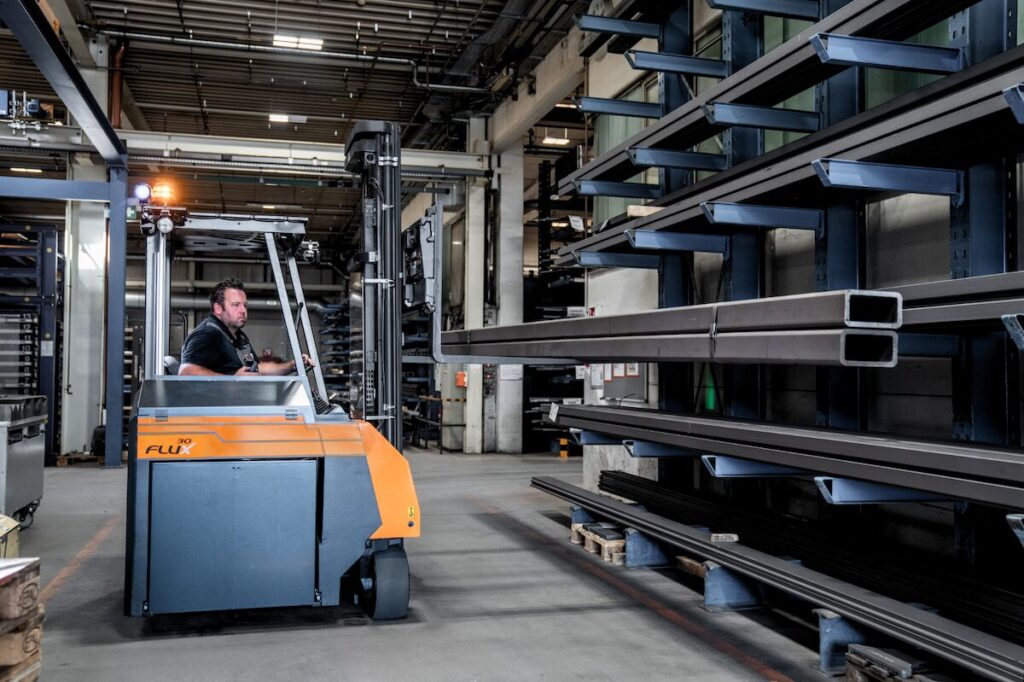
Introducing the FluX 30
The newly launched FluX 30 represents a significant leap in materials handling design. Compact and powerful, the electric three-wheel counterbalance forklift is optimised for both indoor and outdoor use. It combines the functionality of a front loader and a sideloader, making it ideal for unloading trucks and transporting long product through narrow warehouse doorways and into racking systems.
“The FluX 30 is a great little crossover machine. It’s incredibly versatile. It can go from unloading in the yard to block stacking or working in aisles, all with the same unit,” Peatman explained. “And it’s fully electric. With the option of a lithium-ion battery, it is possible to run multiple shift operations on a single battery
What really sets the FluX 30 apart is its patented 360° HX steering system, which allows operators to seamlessly change directions—longitudinal, transverse, even diagonal—without stopping. “That means less tyre wear, less energy use, and more efficient handling. You can literally flick the joystick to change direction while moving,” said Peatman.
Backed by Service
While advanced technology is a cornerstone of Hubtex’s offering, Peatman said it’s the company’s service support that truly sets them apart. “I could talk all day about the quality of the equipment, but what gives our customers peace of mind is knowing we’re there when they need us. Our machines are built to last, but if something ever goes wrong, it’s our fast, reliable service that keeps operations running smoothly. It’s not just about repairs; it’s about being there when it matters most and that’s where we go the extra mile.”
With a strong national presence, Hubtex’s team of highly trained service technicians ensures industry-leading uptime for its customers. Their modern service fleet is equipped with spare parts and diagnostic equipment, and technicians are prepared to fly interstate at a moment’s notice.
“The majority of our staff are technical people, either in the field or in our service department. That’s a deliberate strategy. We want our customers to know they can rely on us—not just to sell them a machine, but to keep them moving,” said Peatman.
Looking Ahead
Hubtex Australia isn’t resting on its reputation. With a growing focus on automation, the company is helping steel businesses explore semi- and fully-automated solutions for materials handling and storage.
“We’re not just selling forklifts. We’re working with steel clients on integrated storage systems and automation strategies that make their operations safer and more efficient,” said Peatman. “That’s where the industry is heading, and we’re ready for it.”
Whether it’s helping a small steel fabricator improve handling efficiency, or supporting a large national stockholder to design a new automated warehouse, Hubtex Australia remains focused on one thing: delivering tailored, reliable solutions that move with the needs of the industry.
As Peatman put it: “We’ve been helping steel companies move forward—literally—for 30 years. And we’re just getting started.”
For further information, visit: https://hubtex.com.au/
Case Study: Atlas Steel
Atlas Steel products vary in size and weight – from lengths of pipe and 1220mm deep sheets right through to packs of steel 12000mm in length, 2400mm deep and weighing over 2500kgs, so it was imperative that flexibility was built into both the layout and the sideloaders.
“Our old building and handling methods were very typical of the steel industry,” commented David, Warehouse Operations Manager of Atlas Steel. “It was dark and not a particularly nice place to work. As with most similar operations we used an overhead crane, which was both expensive to purchase and run, and stored most of the product on the floor or in ‘finger racks’.”
“Handling of goods was a two-man operation using slings which invariably could be both slow and a health and safety risk, so when the decision was made to move into a new building we knew we needed expert warehousing advice, so the call was made to HUBTEX Australia.”
Hubtex Australia proposed a mix of MQ30 and MQ60 Multidirectional Electric Sideloaders, both built with 1300mm platforms so that all machines can operate in all of the aisles. The MQ30, which has a lift capacity of 3000kgs, is fitted with 1200mm tines and primarily handles the 1220mm sheets, stillages, pipe and most of the order picking. The MQ60, with a lift capacity of 6000kgs, is fitted with telescopic tines that extend to 2138mm when handling the larger 2400mm deep sheets in the oversize aisle, and then retract to 1200mm when required to work in the smaller aisles.
So six years on, has it been a success? “Without a doubt,” concluded David. “We have created a whole new culture which has resulted in a 50% increase in operational efficiencies and a fantastic health and safety record. The old way of using the crane and slings was slow and unsafe and could take three men up to two hours to unload a semi-trailer of the larger sheet.”
“With the Hubtex MQ60, one man can unload it safely in 20 minutes. We have become totally reliant on the Hubtex products, so only having a handful of breakdowns despite operating 80 hours per week has been a huge benefit to the overall success of the Atlas Steel operation.
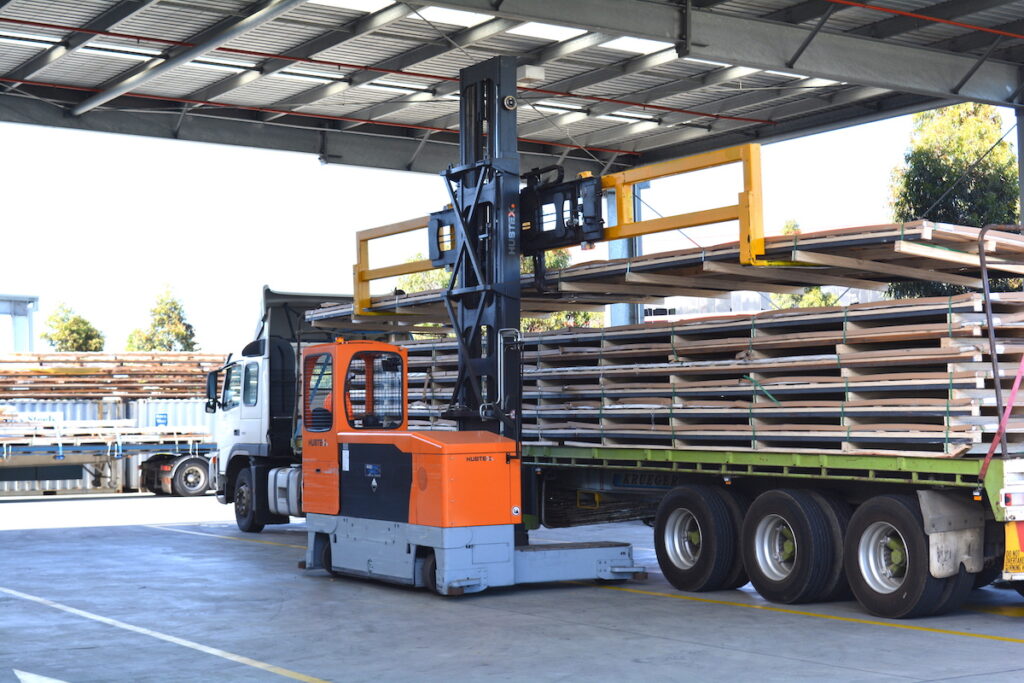