From rural beginnings in the 1950s to a trusted national supplier for major infrastructure projects, the Hayman Group has built a reputation on quality, reliability and innovation. With a focus on Australian manufacturing and engineering excellence, the business continues to evolve—investing in cutting-edge technology and nurturing the next generation of skilled workers.
With a legacy that stretches back to 1953, the Hayman Group is one of Australia’s most trusted names in engineered steel products and fabricated structures. What began as a small business supplying horseshoes and fence fittings to rural New South Wales has grown into a multi-division manufacturing enterprise serving critical infrastructure, utilities, transport and power generation industries across the nation.
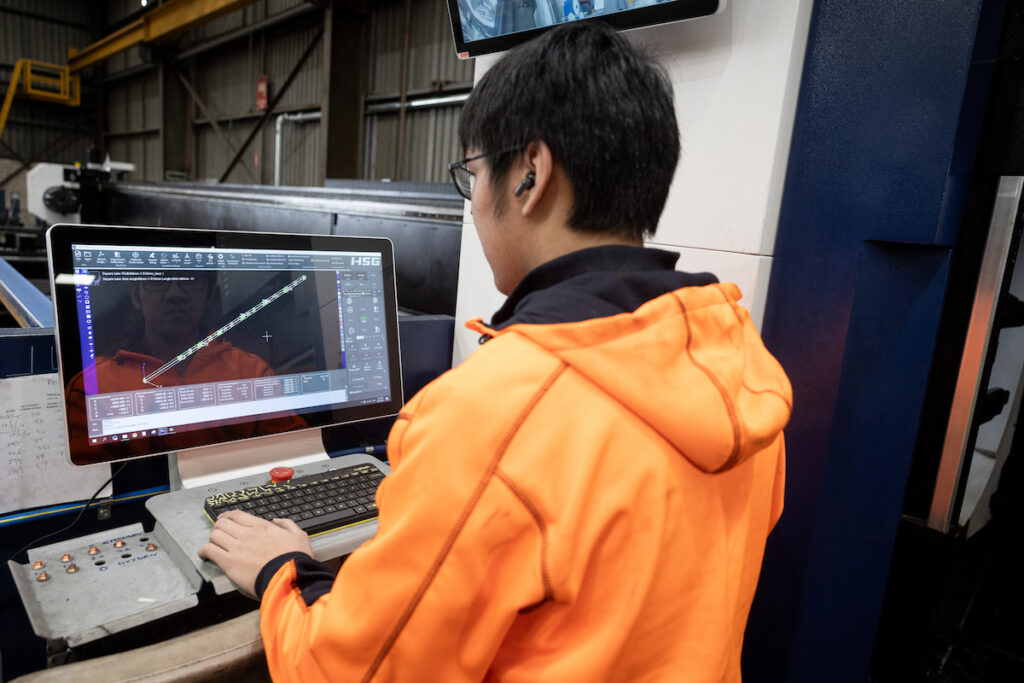
“Our roots are humble, but the mission has always been the same—serve customers with integrity and deliver quality products that stand the test of time,” said Eric Durbin, managing director of the Hayman Group.
Today, the Hayman Group comprises two major divisions: Hayman Industries, which focuses on locally manufactured steel components for power authorities, traffic and road infrastructure; and Hayman Engineered Structures, a specialist division established in 2023 to meet rising demand for complex steel pole solutions in renewables, lighting, and transmission projects.
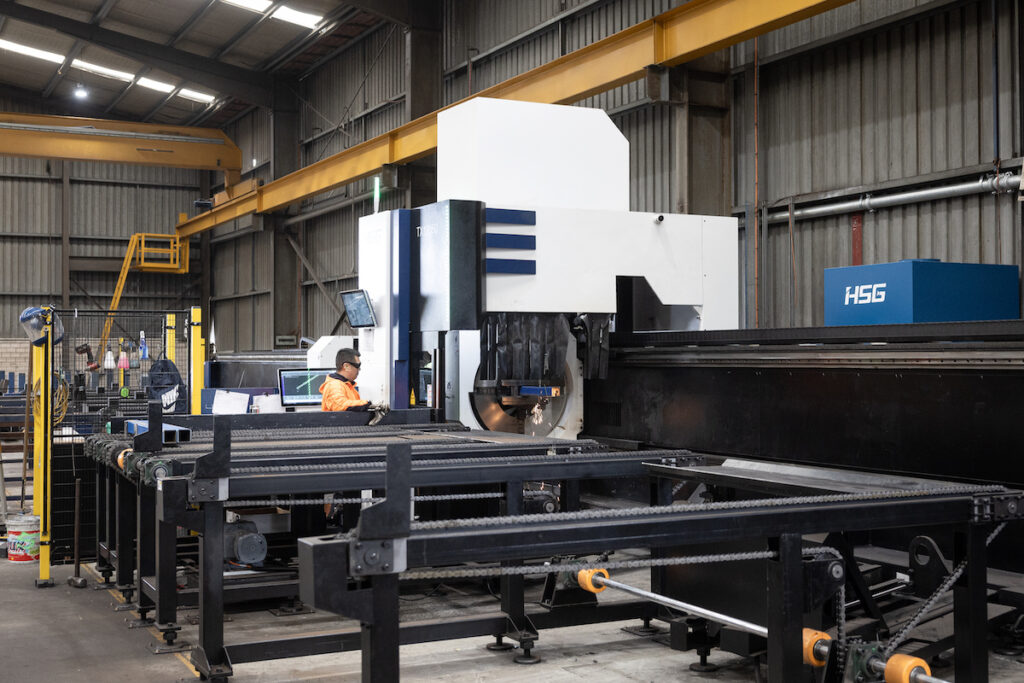
A legacy reforged for the future
Durbin took over the business with his partners 13 years ago. Their vision? Expand geographically and diversify into new markets. “At that time, Hayman was still very NSW-centric,” he explained. “We’ve grown steadily into Victoria and Queensland—we’ve had an Energex contract now for close to a decade—and we’ve strengthened our wholesale capabilities.”
Hayman Industries manufactures a wide range of precision steel products—from cross arms and pole top brackets to specialised fittings for transmission lines, roads, and power networks. The company holds long-standing contracts with major utilities and road authorities, thanks in part to its AS/NZS 5131 CC3 accreditation, and its proven ability to meet the rigorous compliance and quality standards required for public infrastructure.
“We’re in a niche space. Entering this market isn’t easy—it takes time and commitment to earn and maintain those certifications,” said Durbin. “But it’s what keeps the quality up and the fly-by-nighters out.”
Engineering innovation
The creation of Hayman Engineered Structures marked the group’s move into more advanced structural solutions. This division offers fully engineered steel pole systems for floodlighting, transmission lines, telecommunications and more—backed by decades of collective experience and supported by cutting-edge design tools such as PLS Pole, Multiframe 3D and Inventor.
With access to one of the world’s largest pole manufacturers for offshore supply and local project management and quality assurance, Hayman Engineered Structures can deliver end-to-end solutions that meet Australian design standards without compromise.
“We’ve worked on some significant lighting and power projects across Australia and New Zealand,” Durbin noted. “Having the right team on the ground here—people who understand local compliance and engineering—is a huge advantage.”
Investing in technology and capability
A hallmark of the Hayman Group’s recent success is its forward-thinking investment in both leading-edge manufacturing and non-destructive testing technology, as well as mobile contracting services.
The company has established an innovative on-site pole testing service, capable of mapping an entire steel pole, including below ground, to rapidly produce an accurate corrosion map and structural report, allowing ongoing evaluation and management of infield assets.
Most notably, Hayman Industries has installed a state-of-the-art tube laser cutting machine—a major upgrade from its ageing drill line and a leap forward in efficiency and output.
“We’ve recently invested in a tube laser cutting machine, which represents a significant upgrade from the older drill line technology we had when we first acquired the business,” explained Durbin.
“The previous system was becoming increasingly costly and time-consuming to maintain. So, we asked ourselves—if we’re going to invest, what’s the right piece of equipment that not only meets our current needs but also opens the door to new opportunities?”
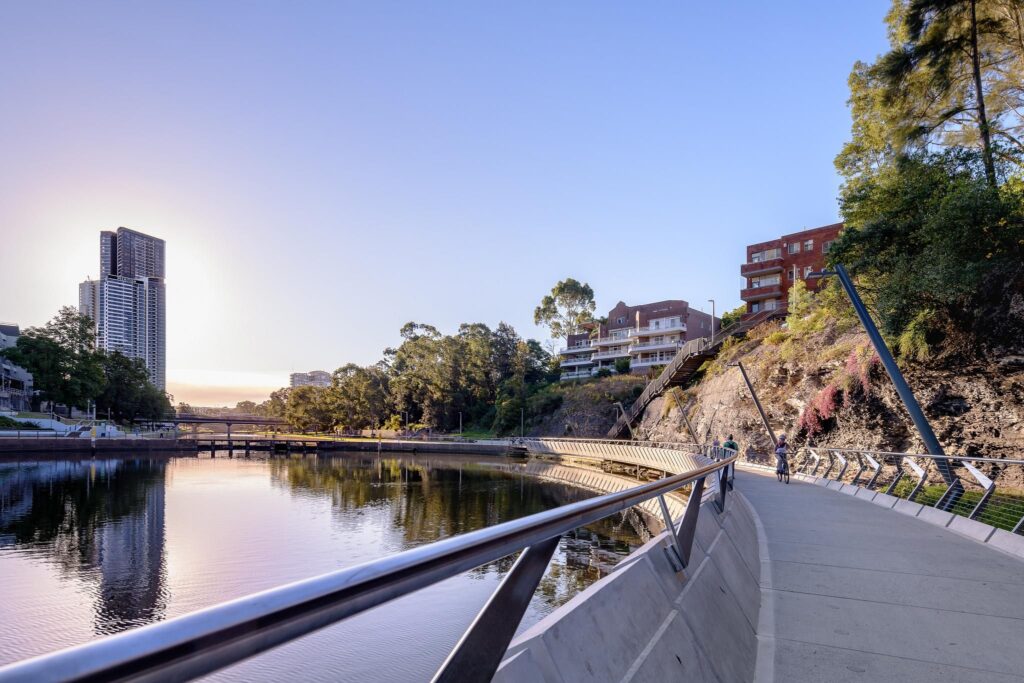
After exploring various technologies, including plasma drill lines and flatbed lasers, the team identified tube laser cutting as the next logical step. “We looked closely at the quality of output and the versatility of the machines available,” said Durbin. “The key for us was also having local support—someone we could rely on for quick maintenance or breakdown service if needed.”
Hayman selected a machine with a 550mm diameter cutting capacity and 12m infeed and outfeed, allowing for much larger and more varied materials than standard 6m or 8m bed lasers. “We deliberately went bigger. Not only does it cover everything we currently do, but it gives us the capacity to branch into new areas,” he added.
The benefits have been immediate. “The machine does everything the old line could, but it’s faster, more efficient, and produces a far higher quality finish,” Durbin noted. “We also invested in automated feed-in and feed-out tables, which means we can now talk to major players like Southern Steel about high-volume processing work—something we just couldn’t have done before.”
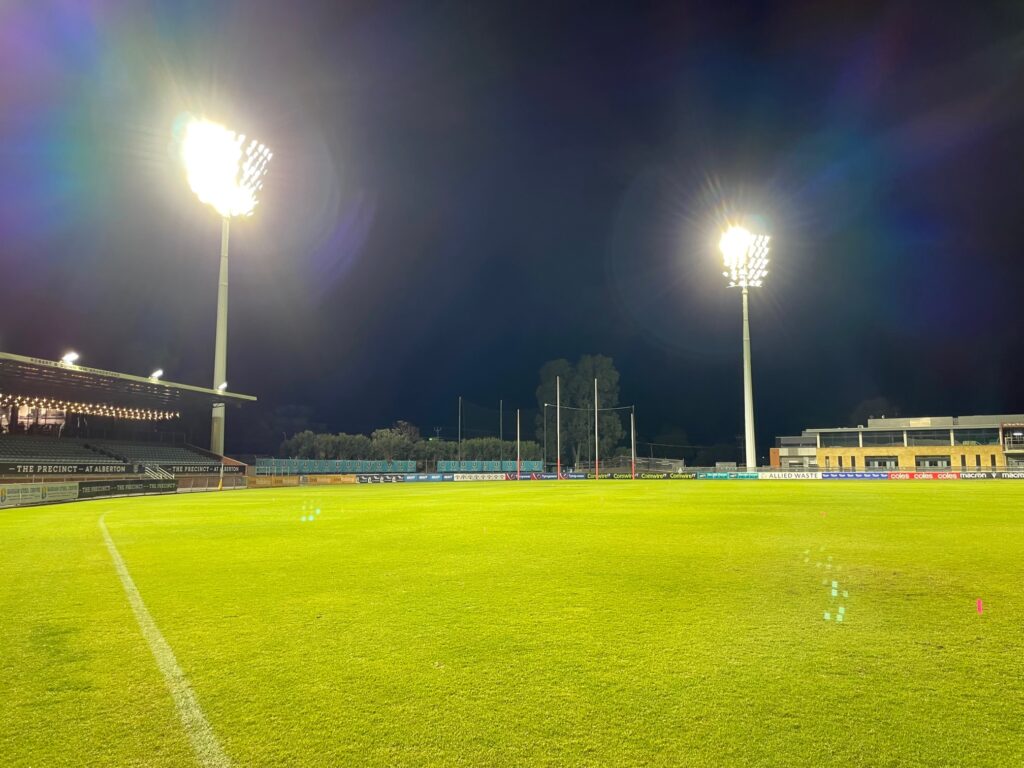
With the extra capacity, Hayman is now providing processing services for other fabricators and steel suppliers. “It’s been a quantum leap forward in technology for us,” Durbin said. “It’s not just about improving what we already do—it’s about creating new opportunities.”
The machine has already proved its worth on several recent projects, including a lattice tower assembly job where Hayman was able to fabricate additional or damaged components in-house, without delay. “Being able to respond quickly and keep the project moving—our customers did not experience any time delays. That’s the value we bring.”
A people-first culture
While technology plays a vital role in the business, Durbin is quick to point out that people remain its greatest asset.
“We’ve got team members who started here straight out of school and have been with us 40 years,” he said. “We’ve created a really strong working environment with low turnover—and that’s rare in manufacturing today.”
This commitment to people extends to the future workforce, too. The Hayman Group actively invests in apprenticeships to address the skills shortage in Australian manufacturing. “We’re doing our part to bring new talent into the industry,” said Durbin. “I came from a trade background myself, and there’s nothing better than seeing young apprentices grow their skills and become part of the team.”

A call for local recognition
Despite its success, Durbin is candid about the challenges facing Australia’s steel industry—particularly the lack of recognition for businesses like his that are investing locally but often overlooked for large-scale projects.
“We hear a lot of talk from the federal government about bringing manufacturing back onshore, but we’re still seeing the big jobs—and the money—go overseas,” he said. “We’ve never taken a handout. We’ve built a sustainable, competitive business, and yet we’re not given a fair crack.”
Durbin believes real change will only happen if government agencies prioritise local capability over lowest-cost bids from offshore suppliers. “We’re ready to contribute to major infrastructure like the upcoming Brisbane Olympics,” he said. “But we need decision-makers at all levels to back businesses like ours—those that employ Australians, pay taxes, and invest in the next generation.”
The road ahead
With decades of experience, a skilled workforce, and a renewed focus on automation and engineering design, the Hayman Group is well-positioned to support Australia’s infrastructure boom—particularly in renewables, utilities, and transport.
“We’ve built this business on hard work, integrity, and a customer-first mindset,” Durbin said. “Whether it’s a transformer bracket or a fully engineered lighting pole, our customers know they can rely on us to deliver—on time, to spec, and with quality that lasts.”
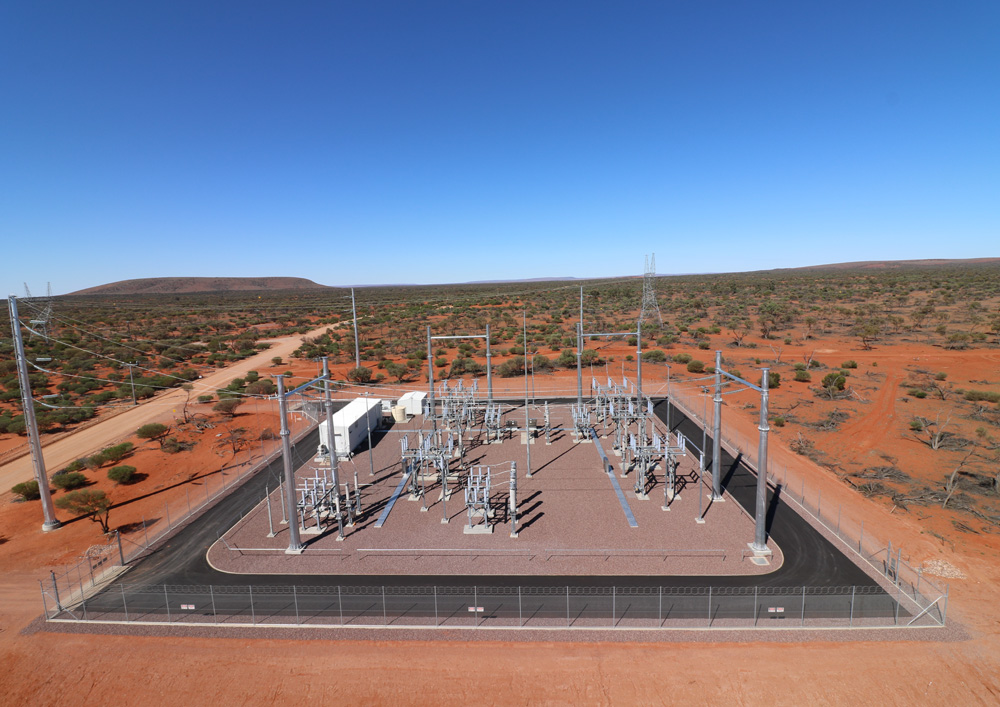