Bekaert is the world’s premier ropes and advanced cords solutions provider. 2023 marks 100 years of specialised experience in steel wire and synthetic rope solutions in Australia. Serving thousands of customers globally and with 17 manufacturing locations around the world, the company’s rope products are designed for some of the most demanding applications across a wide range of industries.
Bridon-Bekaert The Ropes Group was founded in 2016 as a result of a merger between the Bridon Group and the ropes business of Bekaert. Together an unrivalled partnership was created – capitalising on a strong vision, purposeful goals, and centuries of combined expertise and technology leadership.
However, as director Steve Hennessey explained, the company has a long and distinguished pedigree that extends much further back than 2016.
“In May 1920, it was reported that two British investors had met authorities in Melbourne and visited Newcastle with the intention of establishing a works for the manufacture of wire rope products in Newcastle. It was billed as the first of its kind in the Commonwealth. There were some very big names in the rope industry behind the effort, including Haggie and Bullivant and Co.”
“In 1923, the business that 100 years later would become Bekaert Wire Ropes was registered as Australian Wire Ropes Works.”
“Cleverly, that same year, the tariff board was lobbied and a tiered duty system was implemented on imports starting in 1923 to prevent prejudice against locally made products to encourage local manufacturing,”
Steve said.
During 1924, with the assistance of British Ropes, the first stage of the factory was built and commissioned, and the first ropes produced. In early 1925, the first locally manufactured ropes (made from imported British steel wire) went to market.
“Output for the first six months was around 200 tonnes. Today we target more than that every week Before the first six months of production was complete, an additional seven rope making machines had been ordered.”
“After a turbulent few years of feed shortages and trade decline, the first formal supply agreement was signed with Rylands Bros in late 1926, Rylands were a local nail and wire manufacturer. This was the beginning of the InfraBuild relationship that is still in place today. By 1933, Bridon-Bekaert was a fully-owned subsidiary of BHP. Improvements in wire quality by Rylands Bros was providing improved wire rope performance capabilities.”
“With the outbreak of WWII, many of our employees had either enlisted, were drafted, or had been mandated to stay within the steel industry. As a result, women filled many vacancies. To meet the added needs of the defence forces, weekly production was increased to 130 tonnes and rising,” Steve said.
Playing a role in nation building
In these early years, the company was involved in major nation-building projects, such as the Snowy Mountains Scheme.
“In 1951, via distributor Bullivants, large and ongoing orders were received for supply to the Snowy Hydro project, which, at the time, was consuming much of New South Wales’ capital resources.”
With BHP consolidating its operations in 1958, Australian Wire Rope Works became a part of the Australian Wire Industries. The mining boom of the 1970s saw the company invest over $1.5 million in advanced machinery and additional capabilities. Incredibly, this decision proved pivotal as it provided the equipment that enabled the ropeworks to be one of the leading mining rope manufacturers into the next century.
“The quality of this machinery is evident with some still operating today, having been upgraded with the latest electrical and safety technology.”
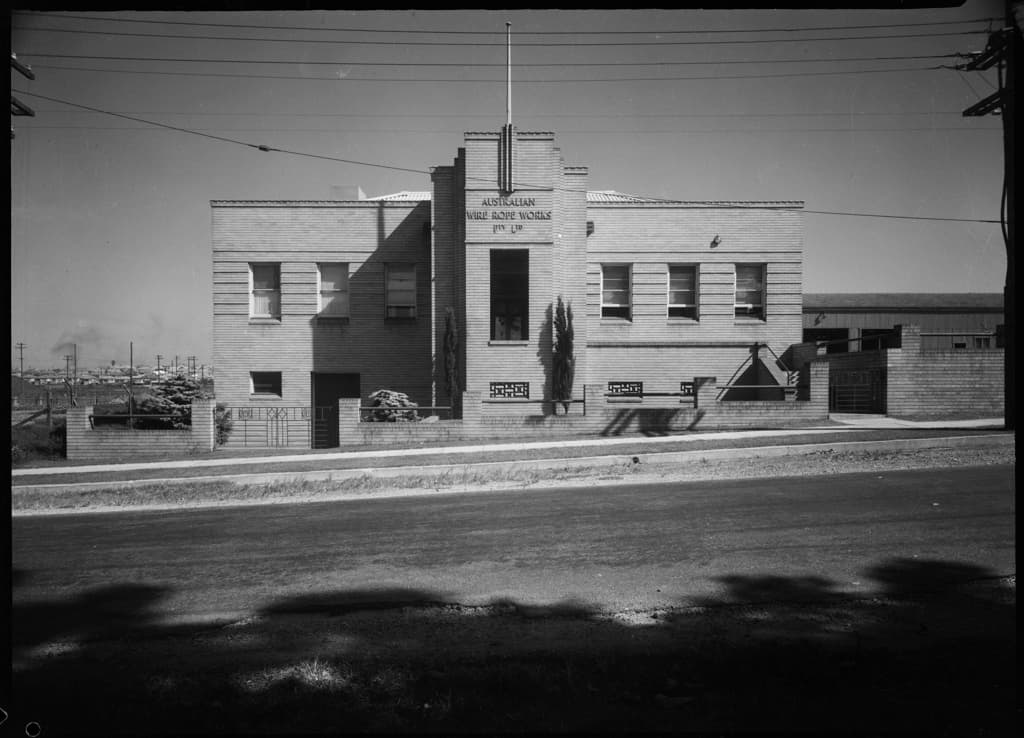
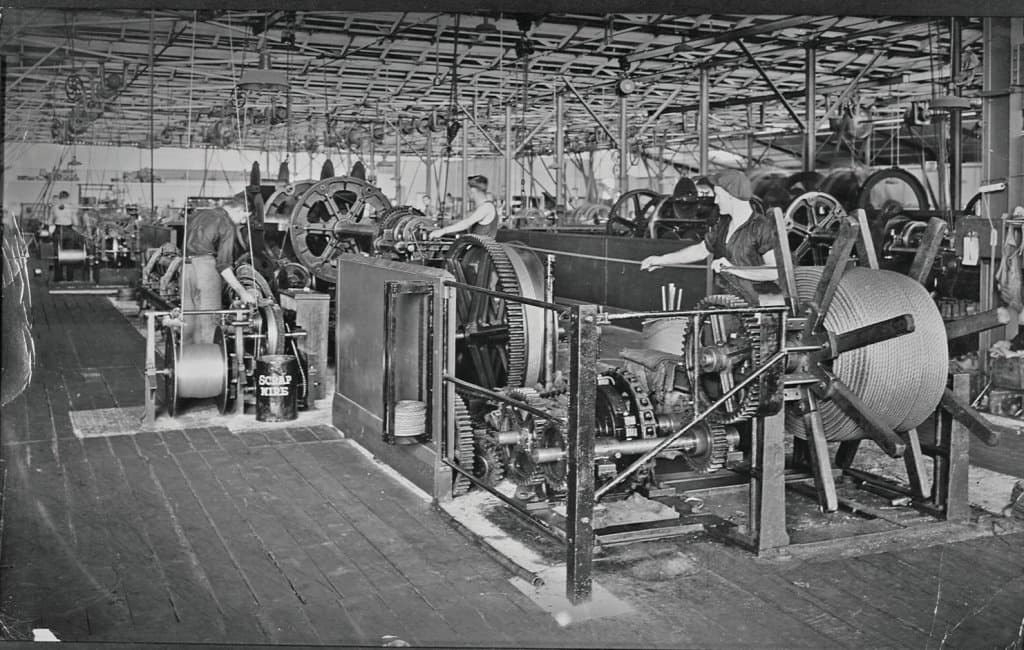
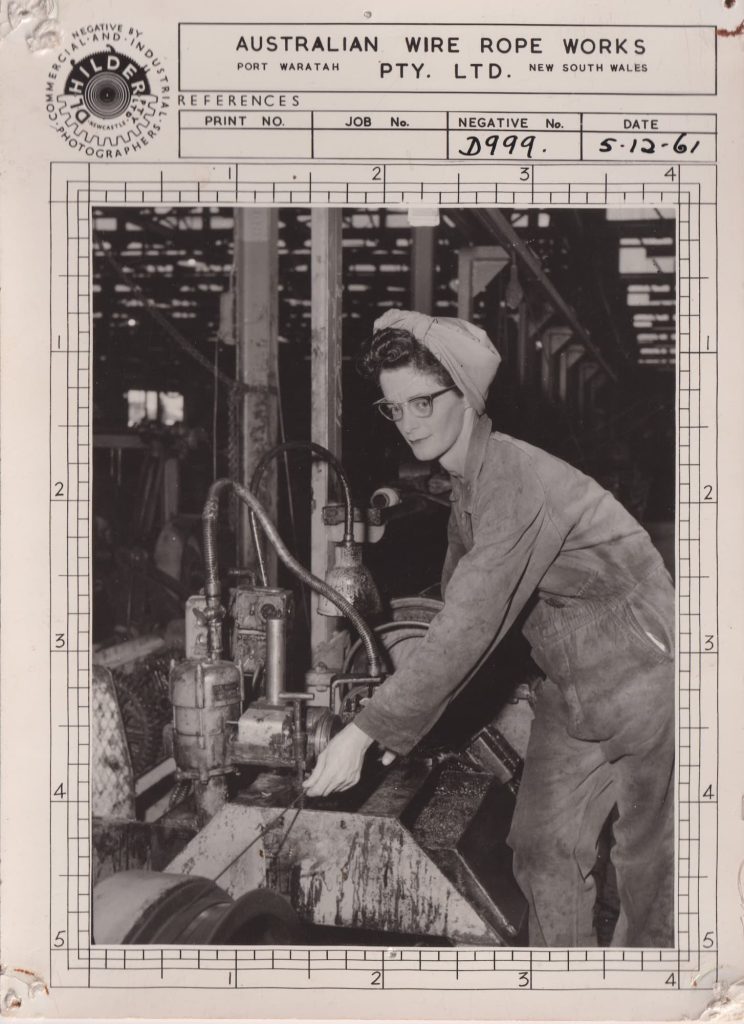
A new chapter
A new chapter began in the year 2000 when, as part of the BHP spin off, the business became known as OneSteel Wire Rope.
“In 2002, the ropeworks became the recipient of one of OneSteel’s early large investments. At the time, market trends had indicated that eight strand ropes would become the dominant mining rope product. To meet the expected demand, the rope closing machine CM3 was designed and installed at a cost of over $15 million dollars. It was commissioned in 2004.”
“This cutting-edge machine provided capability for production parcels up to 150 tonnes in diameters of up to a massive 200mm. This significant step forward in ropemaking technology has proven visionary and one of
today’s business’s biggest strengths,” Steve said.
In 2007, at a cost of $7 million, another game changing technology was developed. An extrusion line for the production of polymer impregnated ropes was installed, which provided the capability for today’s very high-performance shovel rope products.
In 2010, the company became part of the global mining consumables business of Moly-Cop.
“After significant research and development, in 2013, the Raptek facility was opened for the manufacture of a revolutionary new dragline rope product that significantly improved safety for our customers’ maintenance personnel,” Steve said.
“In 2015, Arrium sold the business, and it became the sole Australian facility for global Belgian wire manufacturer Bekaert. A year later, a merger with English ropemaker Bridon International brought us together, creating one of the largest rope manufacturers globally.”
Australian-made high performance steel wire ropes
Today, Bekaert provides steel wire ropes for some of the world’s largest companies across every industry – including onshore and offshore oil and gas, underground and surface mining, cranes and industrial, structures, fishing and marine, cableways and forestry.
The company offers a broad range of high-performance mining products on a short lead time. In addition to rope manufacturing, they also custom design rope solutions, provide rope inspection services and technical support, and have a NATA-accredited testing laboratory.
Bekaert relies on Australian suppliers throughout their supply chain with little imported or recycled steel in their ropes. Their products are made from InfraBuild or Bekaert wire and transformed by the company’s sophisticated facilities in Newcastle by a 155 person team.
“We have an eight-strand 150 tonne capacity rope making machine with capability that extends up to 200mm diameter ropes. We also have a polymer injection line capable of producing 130mm diameter ropes,” Steve said.
Bekaert has an in-house team of technical experts and engineers that is on-hand to assist all their customers. As Steve explains, this delivers even greater value to their customers, “Our team of in-house engineers designs all of our ropes. This means that they have an in-depth understanding of the capabilities of our ropes. So, when customers require good advice, we have the right people.”
While most of the industry was downsizing during the pandemic, Bekaert invested in cutting-edge technology to support its growing operations. In 2021, they opened a new market in port and tower cranes with the installation of a state-of-the-art service centre that delivers the capability to cut, terminate, and test products manufactured by sister Bekaert factories.
The Bekaert Technology Centre (BBtec) is equipped with unique equipment for testing steel and synthetic ropes and wires. It has extensive forensic analysis laboratory facilities and specialists capable of conducting detailed forensic evaluation of new or retired ropes.
“BBtec is our centre of excellence for rope technology development, testing, analysis and verification. BBtec accelerates Bekaert’s new product development, involving the latest rope technologies to increase safety, performance and operational life of ropes working in demanding and hostile environments typical to our core markets in the oil and gas, mining, and construction sectors,” Steve said.
Ready for the next century
After 100 years of delivering quality products, Bekaert shows no signs of slowing down – with major plans to make the most of emerging opportunities in the steel industry.
In line with their vision for the future, the company is investing in a further upgrade of their facilities, to increase its capabilities to cut and terminate high performance Bridon ropes, typically for crane and winching applications, as well as provide ongoing development of polymer infused ropes.
“Through the many historical sources, it is very evident that although we have been through the highs of prosperity and lows of wars, the odd financial crisis and even pandemics, we have survived where many didn’t,” Steve said.
“This is not from having fantastic equipment or an enviable location. It is because we have—and have always had—an incredible team of hard-working, ‘can-do’ people with the ropeworks loyalty and spirit.”
“We proudly produce standard-setting Australian made products that are exported all over the world from right here in Newcastle. We aren’t done yet. We plan to be here for another 100 years,” Steve said.
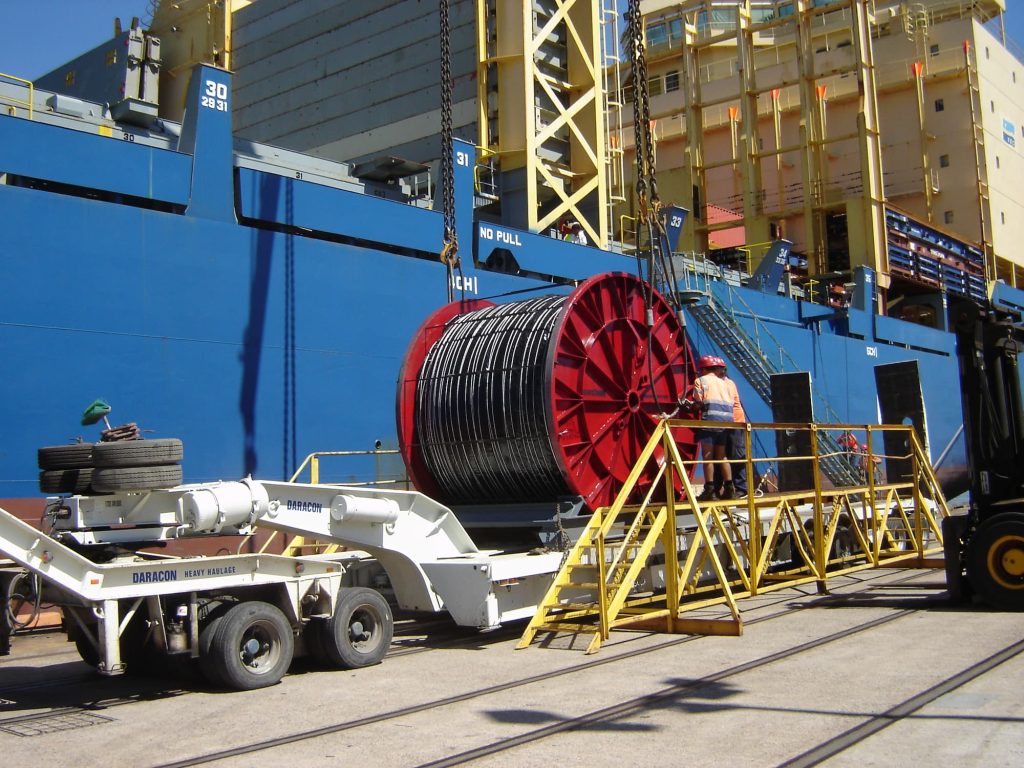