CR Kennedy is one of Australia’s leading distributors of photographic, medical, surveillance, and geospatial equipment. Since its foundation in 1934 as a camera importer, the family-owned company has blossomed into a multi-faceted enterprise, known for its dedicated local support and advanced technological solutions. CR Kennedy is helping transform industries like steel, construction and mining through its digital solutions. With a forward-looking approach that leverages cutting-edge technology like 3D scanning and augmented reality, CR Kennedy is not just adapting to, but leading the charge in the era of digital transformation.
CR Kennedy is Australia’s leading importer and distributor of photographic, medical, surveillance, and geospatial equipment. With offices in every state and capital city across the country, dedicated tech support teams ensure that all equipment supplied can be serviced locally.
According to Bernard Edmonds, segment manager of building construction, the secret to the company’s success is their talented people. “We have a really good infrastructure network of offices and really good team in each office that can not only help with sales, but with backup and support. Our clients appreciate that we’re always willing to go that extra mile to make sure their technical requirements are met.”
With almost 90 years of history, CR Kennedy has established its credentials as a longstanding, trustworthy brand. “In addition to our exceptional service, the general stability of the CR Kennedy business aids our success,” Bernard said. “We’ve been here a long time and we’re not going anywhere.”
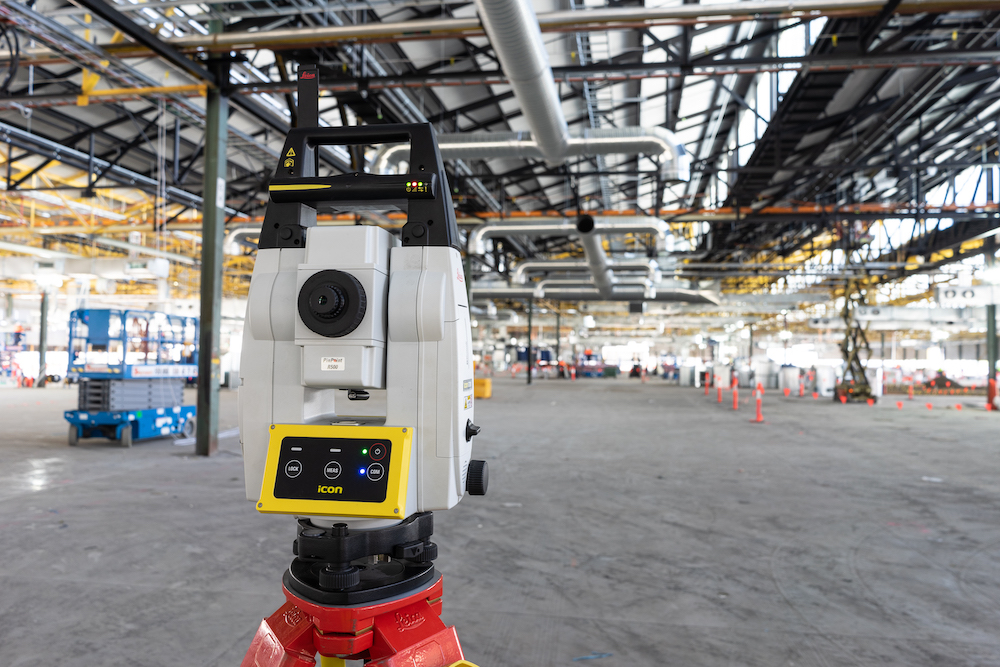
Family owned and operated
CR Kennedy was founded in 1934 by Clement Robertson Kennedy, initially focused on the import of high-end cameras from Japan. After Clement passed away in the 1970s, his son Malcom Kennedy became managing director. Over the past half-century, Malcom has grown the business from a small-scale camera importer into a multi-faceted business that employs more than 300 staff and has a huge turnover. Today, Malcolm acts as chairman as his four sons progress through the company, with Robert Kennedy and his brother Clem as joint managing directors.
“At its core, CR Kennedy is a family owned company—it is traditional in that sense. While the company has grown in size over the years, it still maintains its traditional family business values.”
A diverse offering and client base
CR Kennedy’s camera division continues to stock retail stores and service consumers. But the business has also added a security division which provides high-tech solutions to clients like casinos and supermarkets, and a medical division to deliver cutting-edge instrumentation to surgical wards.
Finally, CR Kennedy’s geospatial division has evolved and grown exponentially since its launch 30 years ago. “We began as a basic importer of survey equipment, concentrating solely on servicing the requirements of professional land surveyors,” Bernard said.
For the last 22 years, the company has been the sole and exclusive distributor in Australia for Leica Geosystems, selling a wide range of products from robotic total stations
to ground penetrating radar, and high definition 3D scanners, to industries as varied as steel, construction, and mining.
“The diversity of our product offering, and hence the customer base we serve, has grown beyond our traditional base,” Bernard explained. “We work with steel detailers, architects, engineers, and concreters—across all aspects of the steel supply chain.”
“Our products are now commonplace on all manner of projects, from residential to high-rise developments, through to the construction of freeways where our 3D automated machine control solutions can be found installed on heavy machinery such as excavators and graders.”
For industries that have traditionally performed measurements and data capture by manual methods, CR Kennedy’s digital solutions are transforming their processes by replacing tape measures and notepads. “We provide the full solution from start to finish—the equipment and the software, as well as training and support for all these solutions,” Bernard said.
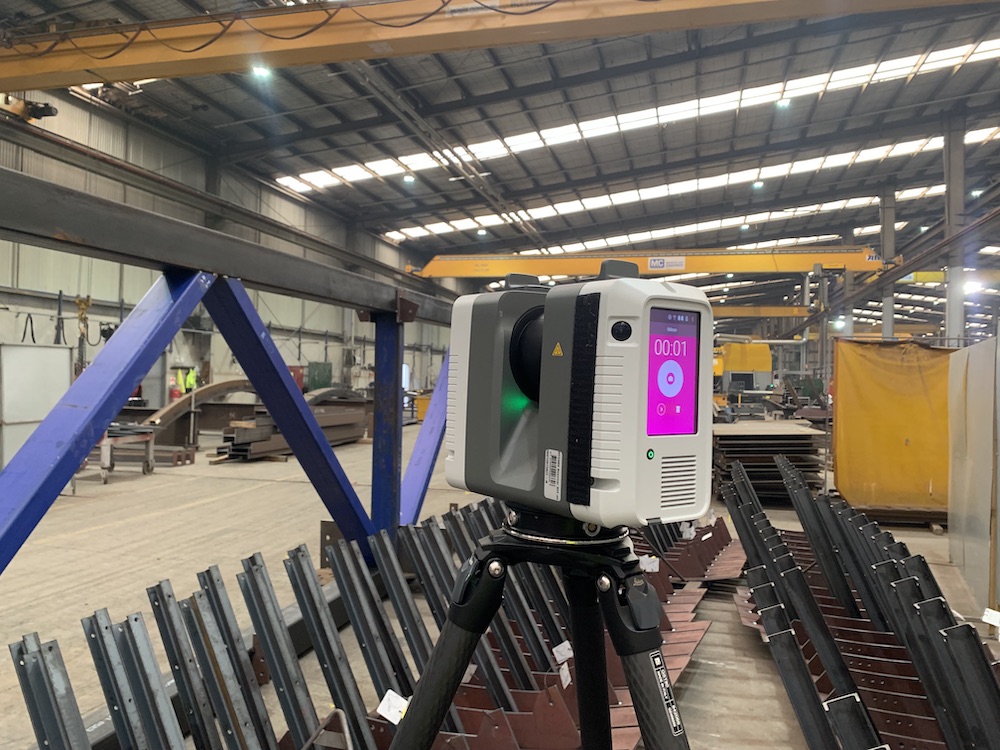
Watkins Steel implements laser scanning
Watkins Steel is a traditional steel fabrication company based out of Brisbane. For over 50 years of operation, managing director Des Watkins was of the mindset that innovation was impossible in the steel industry.
That all changed in 2013 when the business embarked on a digitisation journey that encompassed laser scanning, drone scanning, 3D photogrammetry, augmented reality, and virtual reality. With the introduction of robotics, Watkins Steel engaged CR Kennedy to implement laser scanning. “Robotics is only as
good as the information we’re feeding it,” Des explained. “By accurately turning the site into a digital footprint, we had all the measures we needed.”
Leveraging 3D visualisation and automation, the business has reduced factory labour by 3,000 to 5,000 man hours per month – while minimising the risk of human error. Thanks to the technologies they’ve implemented in partnership with CR Kennedy, the company has expanded to become Holovision, a leading provider of spatial data and digital engineering solutions.
Des said, “Rather than just being a steel fabrication company limited to south-east Queensland, we’ve now got Holovision in Melbourne, Mackay, and Darwin – and each office is growing. With a staff of about 100, there are 20 people that are doing jobs that didn’t exist not that long ago.” The results speak for themselves: in the past year alone, Holovision has grown by about 50%, up from 20% year on year. The company is constantly upskilling their staff to ensure that everyone in the team knows how to laser scan and import data into other platforms like augmented reality and virtual reality.
“What we have found is that laser scanning is the underlying platform that we’ve now been able to feed into virtual reality and augmented reality. It’s opened up these whole new fields. Now we’re scanning things and working on other projects that have nothing to do with steel. From humble beginnings, thanks to CR Kennedy, we’re now going overseas and I’m so excited by it.”
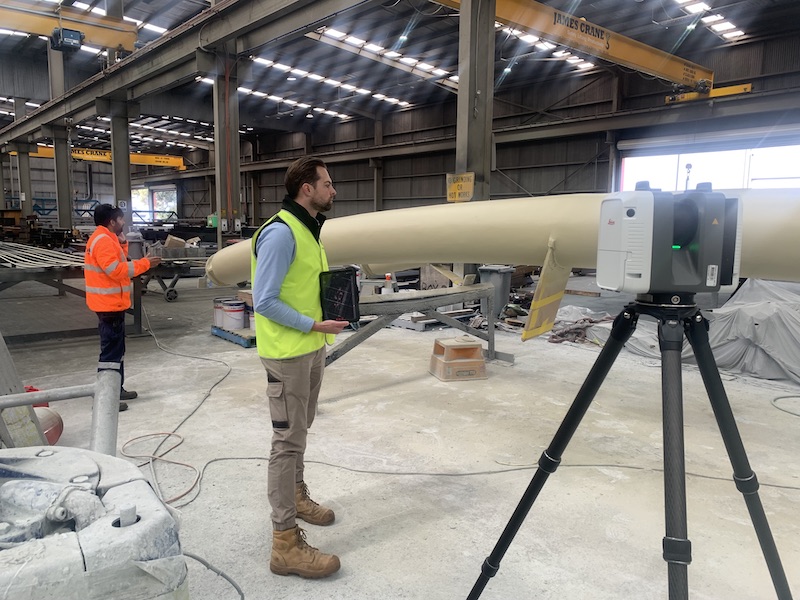
Bringing the digital 3D world to the steel industry
With laser scanners enabling a seamless transfer of data, Bernard Edmonds, segment manager of building construction at CR Kennedy, is excited about the opportunities that this new way of working will create for the Australian steel industry. “The ability to work within a 3D environment across the whole spectrum of design, fabrication and installation, and then back to the design phase once the construction is finished is a gamechanger,” he said.
Previously, a design would be completed in an office environment to a high level of specification. But once the steelwork was delivered to the site, and beams and columns were erected using tape measures and string lines, things could always go wrong.
Now, with the availability of robotic total stations, accurate 3D placement and set out of these structures takes away the risk of human error and allows fast, efficient work to be carried out with very low risk of any rework to be done. On completion, a laser scan of a newly constructed building ensures that the model is up to date with what has been installed on site – not just what was designed.
Bernard said, “With digital solutions like those supplied by CR Kennedy, the likelihood of errors is greatly reduced, rework is no longer a common
Bernard said, “With digital solutions like those supplied by CR Kennedy, the likelihood of errors is greatly reduced, rework is no longer a common occurrence and steelwork need not be torn down and replaced. CR Kennedy is able to contribute to construction efficiencies, helping ensure that projects are completed on-time and on budget.”
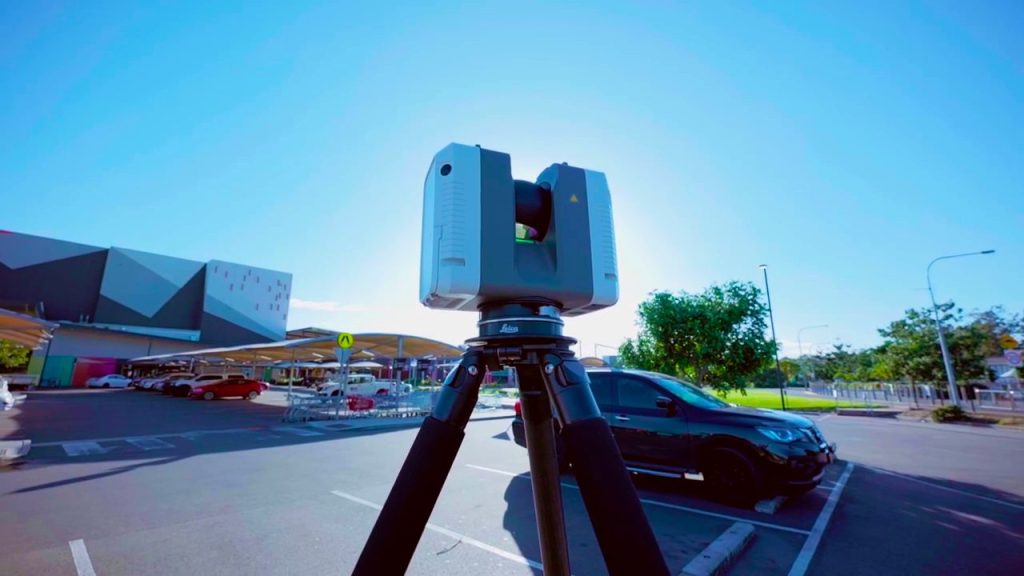
Living the future every day
As technology becomes more capable of handling huge data sets extremely quickly across the whole lifecycle of construction, designs have the potential to be improved and enhanced even further. The CR Kennedy team is also preparing for a wider usage of augmented reality and virtual reality in the steel space, particularly when it comes to setting out features on a site.
“You will be able to put on a headset and analyse anything within the designed 3D model as you walk around a construction site – a concrete wall, the edge of a slab, holding down bolts. The automation in layout and scanning technology is only getting better and better as well.”
But one thing is clear for the organisation: the days of working with 2D paper drawings are well and truly over. “I feel like we’re living the future every day – every day the pace of technological advancement keeps us on our toes here at CR Kennedy,” Bernard said.
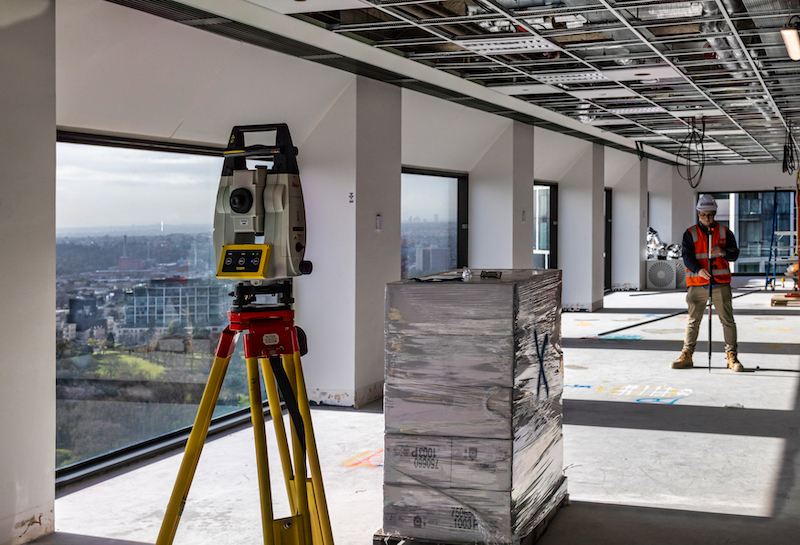
Leica digital setout ensures clash-free steel design
CSD Group Australia was engaged for pre-construction works for the Aldi supermarket at Indooroopilly Shopping Centre in Queensland.
The project involved reinforcing the carpark roof deck below with additional steel supports. Initially CSD Group performed a laser scan and digital measurements prior to detailing the steel supports that will be installed beneath the new store.
Both the laser scan and digital setout were undertaken simultaneously and took just one day. CSD utilsed their in-house Leica iCON Setout Station (iCR85)—purchased from CR Kennedy—to setout all concrete fixings and steel fitting plates.
Back at the office, the laser scans were processed and registered together to produce a complete 3D point cloud of the carpark. The capture included concrete columns, pen marks showing Post Tension (PT) cables, conduit locations in the undercroft of the carpark as well as rebar in the concrete columns. The point cloud was imported into Tekla Structures to begin steel design, avoiding the existing structure and elements.
Despite the architectural design having regularly spaced brackets and beams, the site scan determined that:
Some steelwork had to be redesigned to be installed to the carpark undercroft. The redesign resulted in cost savings, easier installation and faster fabrication while maintaining structural integrity.
All steel was to be fixed to the underside of slab with masonry anchors at 1m centres. We managed to avoid all PT cables as marks (scanned by others) were all picked up. Beams were fixed to existing concrete columns with first fix bracket t-plates, each with six Hilti fixings. All rebar marks were picked up by the scan, so all 16 brackets were modelled individually to miss the rebar. Each bracket ended up being different.
Columns were not square to each other and many rotated. This would not be picked up with a tape site measure. The ceiling is sloping, so the steel is not all at the same level. It was adjusted to make grout between top fix plates and ceiling to a minimum.
The new steel model was re-imported to the point cloud in correct position. Using virtual reality (VR), a “walk through” of the carpark was also done while in the office. The VR enabled us to do a more enhanced clash check between new and existing structures.
Had the site scanned not been preformed, the original structural design would have resulted in extremely low headroom, in some cases below minimum 1950cm floor to ceiling/beam heights for this carpark.