Located near the Moama Wharf, the Horseshoe Lagoon Bridge was an old timber bridge that spanned approximately 115m over the Murray River. Over the years, the timber bridge had suffered ongoing weather damage. As a result, an engineering inspection classified the bridge as unsafe and unable to meet weight load requirements. In addition, the safety and accessibility of the stairs leading to the bridge needed improvement, as did the access to the riverfront, and the wharf facilities for paddle steamers.
With tourism on the rise and the popularity of the region increasing, the Murray River Council decided to decommission the old timber bridge. It was then replaced with an entirely new structure fabricated from over 135 tonnes of hot dip galvanized structural and tubular steel.
Valmont® Coatings provided all galvanizing needed to deliver the new bridge. Based in Melbourne and with over 35 coating facilities in seven countries, Valmont is one of the worlds most respected providers of hot dip galvanizing.
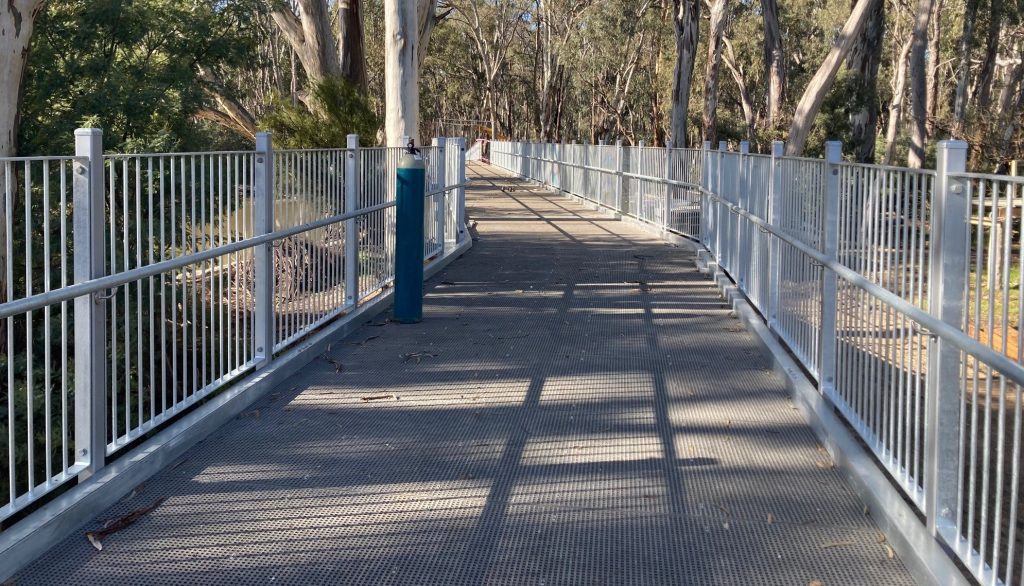
The role of galvanizing
In the early design phase, the bridge was initially specified with a paint finished coating. However, as the project progressed, the design was converted to Hot Dip Galvanizing through the hard work of the fabricator with consultation with Valmont®. The conversion was quite easily passed as it would lead to the most suitable anti-corrosive coating for its environment.
At the early stages of designing the bridge, it was initially specified as a paint finished coating. However, as the project progressed, it became clear that galvanizing was a much better option.
According to Valmont® Coatings sales manager, Marco Bazzano, “The bridge was initially specified as paint. Luckily, Valmont® was involved in the early design stages of the bridge. When the bridge was initially specified as paint, Bendigo Engineering got in touch with us, to ask our opinion. Our team went out to the site for an inspection and determined straight away that galvanizing would be better both from a durability and an aesthetic perspective.”
“The bridge will be subject to general wear and tear, as well as extreme weather conditions. With galvanized steel, once it is installed and erected, you can just walk away and not worry about it. If a section is damaged, it won’t rust, and there won’t be paint peeling off the edges.”
“The years to first maintenance was one of the main reasons the Murray River Council opted for galvanizing. If the bridge had been painted, it would have required yearly maintenance, particularly due to its location—it is prone to damage from wind and trees. Galvanizing was always going to be the best choice.”
In the end, hot dip galvanizing was used across every part of the bridge, including: the 12m 356OD pipes as the supporting pillars; the main walkway structure in the form of straight structural steel with bolted connections; and all other components such as balustrades, handrails and fittings. All the members were pre-assembled in the fabricators’ workshop in Bendigo, loaded onto a truck and transported to Moama in sections.
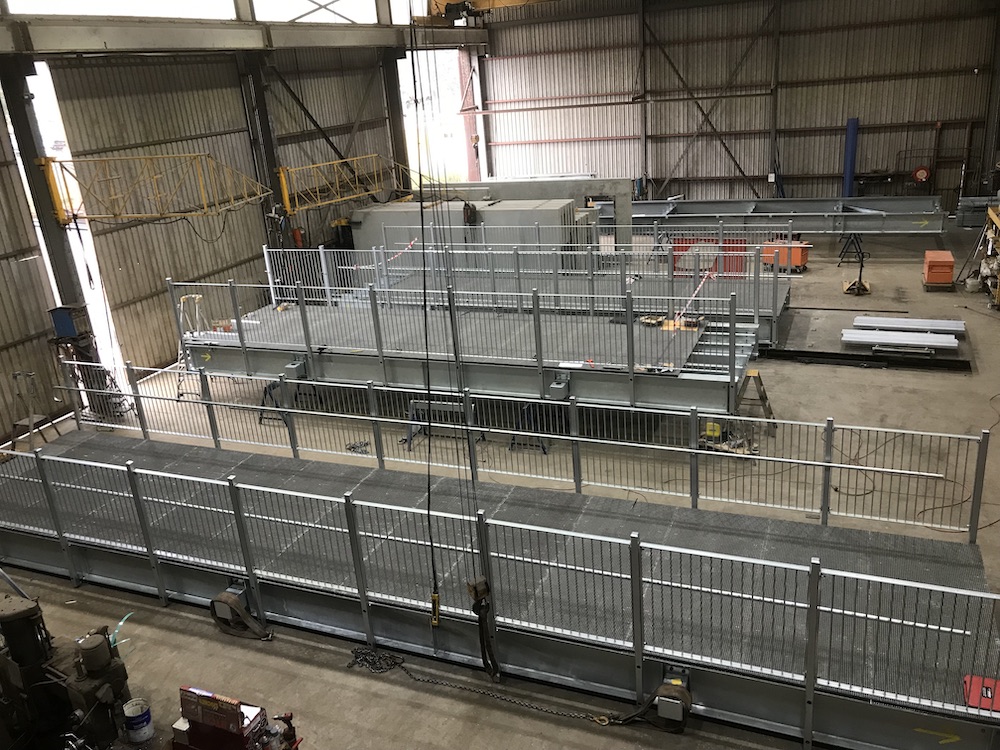
A tight timeframe
The bridge fabrication schedule had very strict timeframes and deadlines; it had to be commissioned in time for the grand opening of the Moama Lights on 31 July 2022.
The ongoing, industry-wide supply and logistical challenges related to steel availability and delivery delays persisted. In addition to these steel supply issues, one of the biggest scheduling challenges was coordinating the sandblasting of the large pipes to remove protective black lacquer prior to galvanizing.
“All the columns on the bridge had to be sandblasted, and the window of time allowed for this was tight. The turnaround from fabrication, to sandblasting, and then galvanizing was all completed on a very tight deadline,” Bazzano said.
“The transportation of the steel from Bendigo to Moama also proved challenging due to a lack of availability of trucks and drivers. Galvanizing proved a better option than paint coatings during handling and transportation. If the steel had been painted, it would have required special handling to ensure it wasn’t marked. This would have slowed down an already tight timeframe.All these timeframe and transportation challenges were easily overcome with good communication between all the project stakeholders and detailed planning and organization,” Bazzano said.
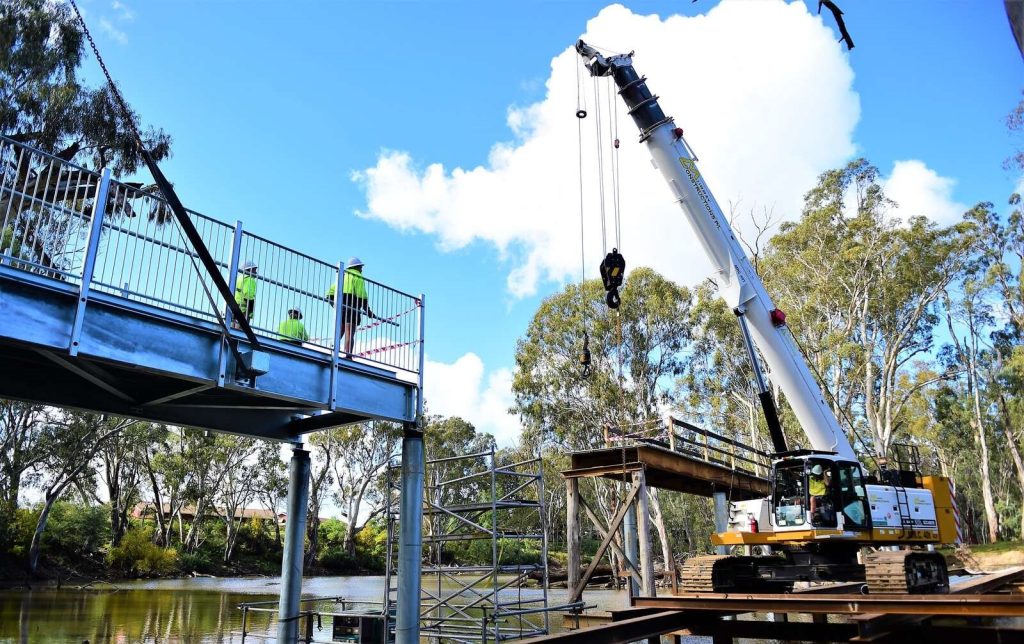
Market potential for infrastructure projects
Galvanizing was the perfect solution for the Horseshoe Lagoon Pedestrian Bridge. This project demonstrates that not only is galvanizing is the most suitable anti-corrosive coating for infrastructure, it is also economical during construction and maintenance, fast to erect, and provides better damage resistance compared to paint. It should encourage Councils to specify a galvanized solution when replacing timber assets that have reached the end of their design life.
“This project has demonstrated the broad spectrum of benefits offered by galvanizing—not only to the Murray River Council, but to other local councils. The construction of another bridge is planned for the other side of horseshoe; it’s a no-brainer to specify galvanizing for this as well,” Bazzano said.
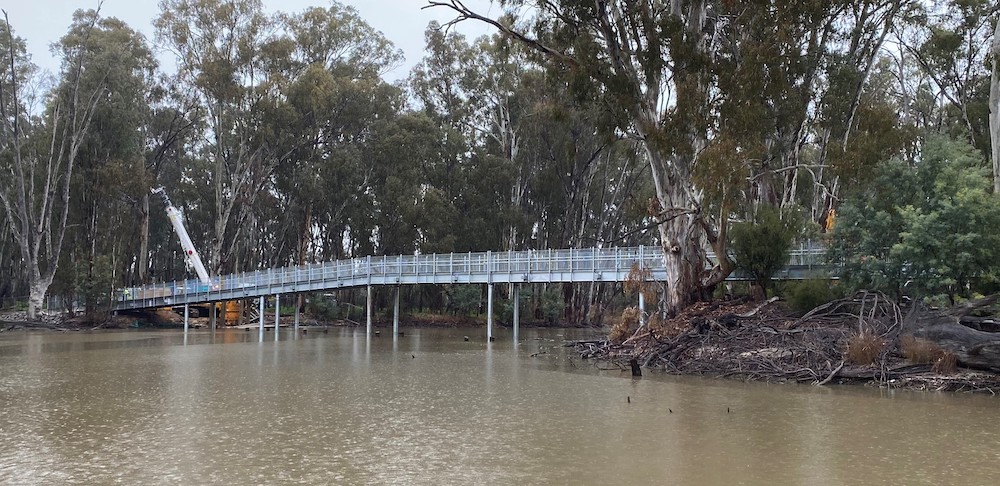
Galvanizing on display
The end result is spectacular. The pedestrian bridge is the centrepiece of the Moama Lights, an immersive lightshow that takes place along the Murray River. The bridge and its quality galvanized metal is on display throughout the show.
“The bridge features in the Moama Lights show and looks fantastic. When it is all lit up at night-time, it is really something special. The lights even change colour as you walk along the bridge. The Valmont® team was really happy to be involved in the whole project. We’ve been overwhelmed with the positive feedback we’ve received as result, particularly due to the light show. During the day, it just looks like a galvanized bridge. At night, it looks like the Eiffel Tower light show,” Bazzano said.
Project team
- Developer and owner: Murray River Council
- Architect: AW Maritime
- Main contractor: Bendigo Engineering Services
- Hot dip galvanizer: Valmont Coatings (Melbourne)
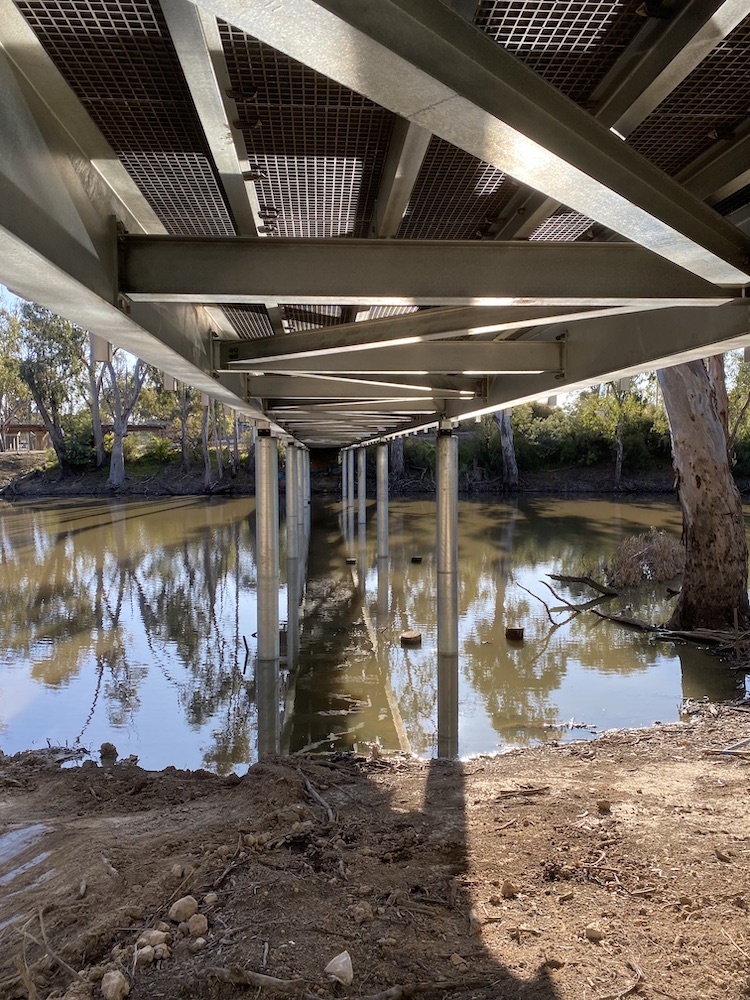