The InQuik bridge system, an innovative modular construction methodology, simplifies bridge building using a steel reinforcing cage and permanent steel formwork. This Australian invention offers self-supporting structures with a minimum 100-year design life and minimal maintenance requirements. The system, which entered the market in 2017, has gained significant local traction due to its easy installation and structural advantages. Collaboration with local firms like SMEC, BlueScope, InfraBuild, Australian Reinforcing Company and Nepean Engineering and Innovation has helped ensure InQuik’s success.
A modular bridge construction methodology, the InQuik bridge system was invented and developed by Bruce Mullaney, Logan Mullaney and Jim Howell in 2015.
The system is based on a standard reinforced concrete bridge methodology, which has been used around the world for more than 100 years. It is currently the most widely used bridge construction methodology in every country, especially due to advancements in pre-casting and tensioning cables.
The key idea behind the InQuik system is that a welded steel reinforcing cage is connected to a permanent steel formwork so that the construction load from the concrete is transferred to the internal reinforcing. Thus, the structure is fully self-supporting and concrete can be poured on-site.
This simple concept has numerous constructability and product quality advantages, and the structure has a minimum 100-year design life (achieved by using 40 MPa concrete, or 50 MPa in a B2 coastal environment), with minimal to no long-term maintenance requirements.
The maximum single span currently offered by InQuik is 18.5m. However, multi-span options are available, using the InQuik headstock to build bridges with no real limit on the total length achievable.
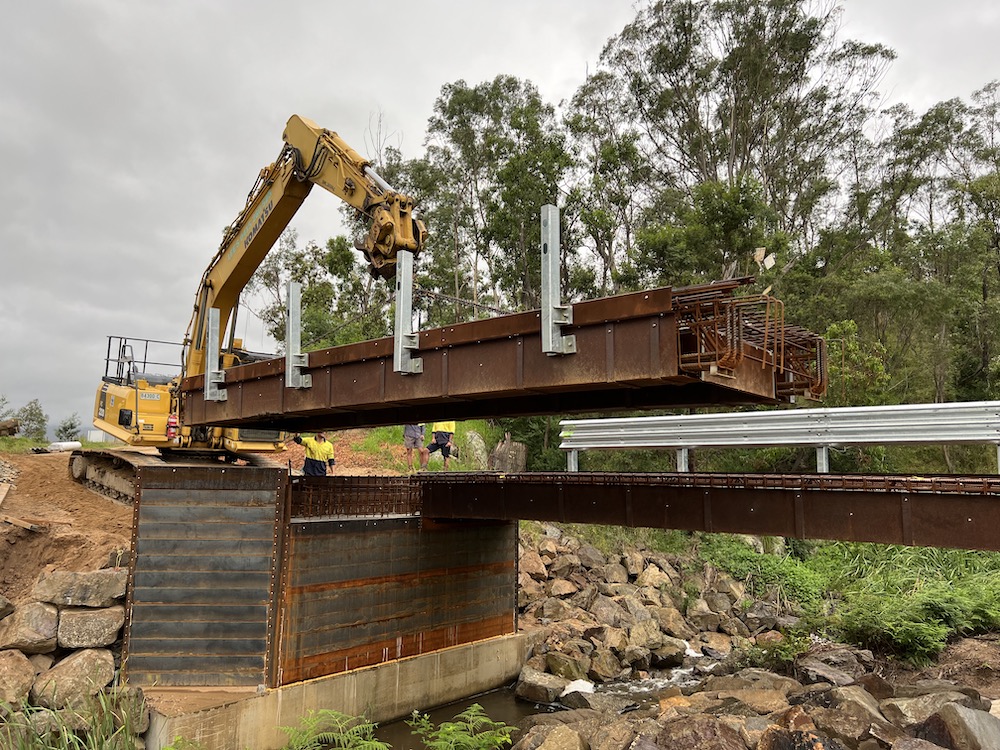
Revolutionising bridge design
As Bruce Mullaney describes it, he and Jim never intentionally set out to revolutionise the engineering and construction of bridges. “My brother in-law Jim and I were developing a new fire-rated high-rise housing system that used concrete suspended floors. When we looked at the drawings, we realised that the system could also be used as a bridge. And so our bridge journey began,” said Bruce.
InQuik was keen to work with other local companies from the outset. According to Logan, “We looked to team up with Australian companies to get off the ground. That’s one of the reasons why, in 2015, we partnered with SMEC—the originally state-owned company that built Snowy Hydro.”
As a result, the InQuik bridge system was designed and certified by SMEC to comply with the requirements outlined in the Australian Standard AS 5100 Bridge design, including SM1600 and HLP (Heavy Load Platform) 320 and 400 loadings, as required.
The system first entered the Australian market in 2017. Since then, it has rapidly gained local market share as the product’s ease of installation and structural advantages are converting customers to using it as their preferred option for new and replacement bridges.
Logan explained how quickly the system has gained traction within the market. “Our first bridge sale was part of the Snowy Hydro 2.0 project—that was the first commercial bridge we ever completed. It only took 12 hours to build, including pouring all the concrete. In 2017, in our first year, we built three bridges. The year after, we built eight bridges. To date, we’ve built more than 200 bridges.”
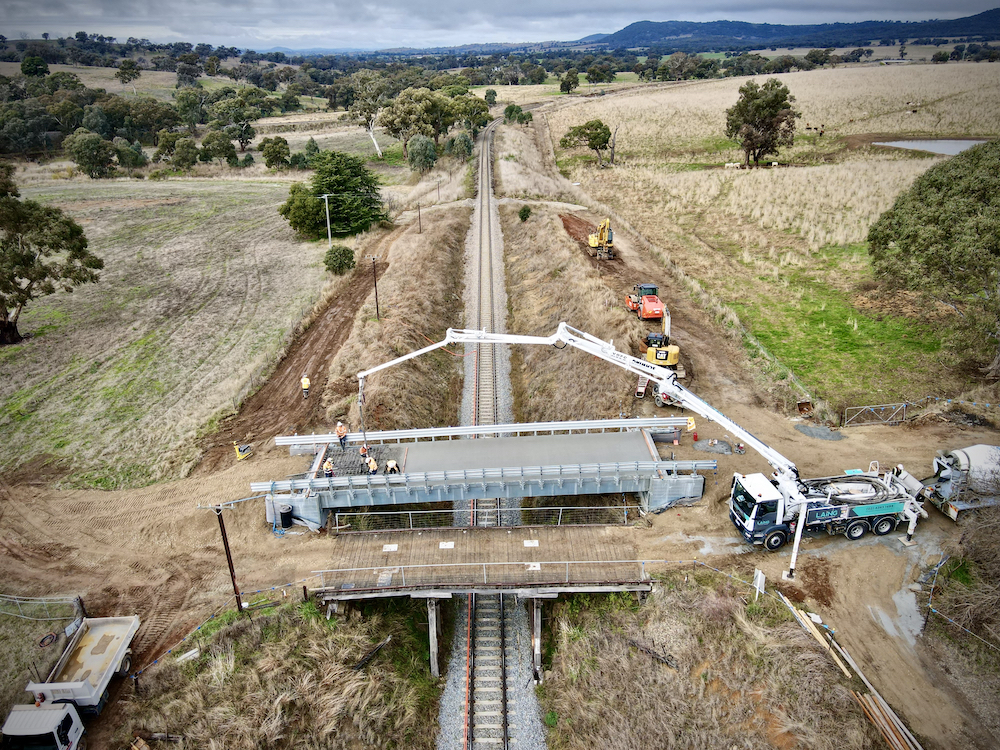
Collaboration with local partners
The InQuik system includes a variety of steel elements, from corrosion resistant steel, through to stainless steel and reinforcing bar. The steel consumption is approximately 70% pre-fabricated steel reinforcement, 25% coated steel product, and 5% stainless steel and ancillary steel elements. InQuik collaborates with local companies to ensure this steel is locally sourced, including leading manufacturers like BlueScope and InfraBuild.
According to Michael Wright, InQuik’s director of technology and innovation, “BlueScope has been fantastic—we work closely with their team. We need steel sheet and plate, of course, which they supply. However, when we moved into the use of REDCOR® weathering steel, BlueScope was particularly helpful, providing technical support around how to handle and weld REDCOR® weathering steel so that it delivers the best possible performance.”
The formwork for the InQuik system can be made from a selection of steels (REDCOR® weathering steel, zinc-alum coated steel, or stainless steel) which each have different corrosion behavior. The most suitable cladding component would be selected based on its corrosion performance in each bridge’s specific environment.
The formwork is left in place for the life of the bridge. More conventional concrete construction uses temporary formwork, which is not typically made from steel and is reusable. The use of permanent steel formwork increases steel consumption of the InQuik system by approximately 20% compared to conventional methods.
As Michael explained, “We currently import the coated steel product used in the formwork. However, we’re working with BlueScope on an Australian equivalent so that we don’t need to import the material from Europe and can use Australian products, which is always our preference. BlueScope has taken us through their mills and given us access to their technical people—their collaboration has been great,” said Michael.
“We have a similar working relationship with InfraBuild, who supply a lot of our rebar. They’ve always been very responsive to our needs and supplying products for us.”
In order to have sufficient steel for the structure to be self-supporting, an additional 25% of reinforcing steel is required compared to conventional methods. Additional reinforcing steel is required for the integral InQuik bridge design where the abutments, decks and wingwall all form a monolithic bulk.The integral design reduces long-term maintenance requirements through eliminating longitudinal deck joints and removes tiedowns and bearings.
These extra steel elements mean the InQuik bridge system required an additional 35% more steel compared to a conventional bridge of this type. Additional reinforcing is consumed and there are numerous stainless steel connectors, supports, and so on used in the concrete cover zone. These steel elements mean the InQuik bridge system consumes an additional 50% more steel compared to a conventional bridge of this type.
InQuik’s collaboration extends into the fabrication process as well. “Nepean Engineering and Innovation has been a very important partner for us. They’ve done a lot of fabrication work for us as we have grown our business. Nepean has been fabricating our structures on their site and shipping direct to our clients. They have a solid understanding of how we make all our components, backed by our technical support on drawings and structures.”
“There is a real willingness in the Australian steel supply chain to get involved and help out. Once you know you’re helping another Australian supplier, everyone is willing to contribute and lend their support.”
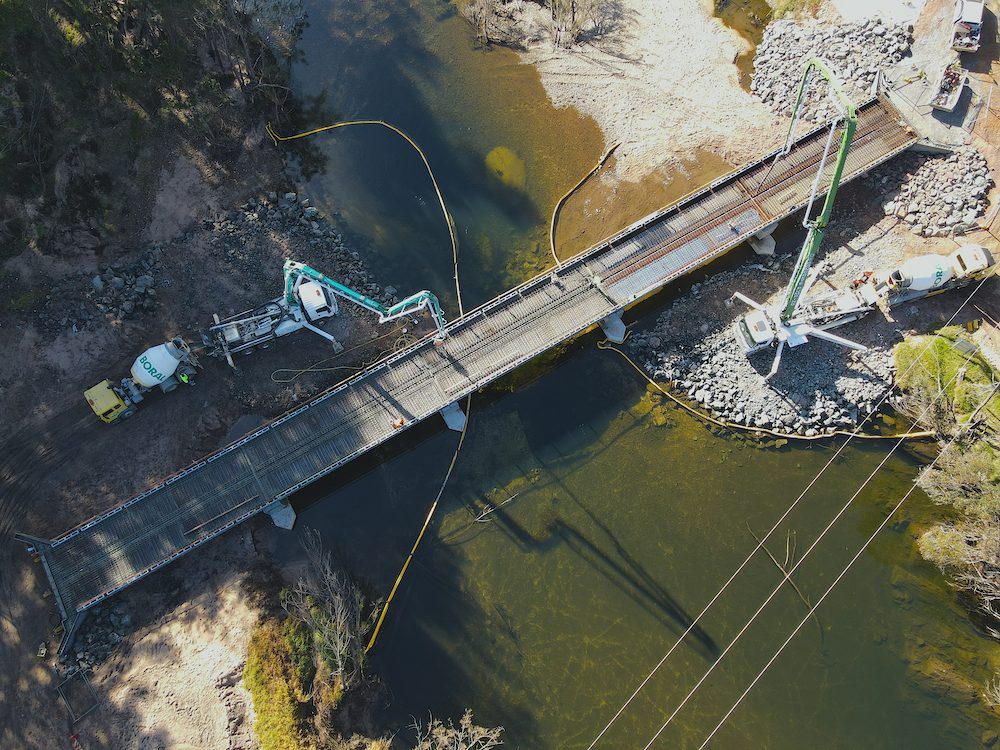
Murphy’s Bridge
Murphy’s bridge was the lifeline that connected the widespread community around Cadgee in New South Wales.
On New Year’s Eve in 2019 as the sky turned purple and red, most of the people fled their home as the bushfire descended. On returning home several days later, the bridge across the Tuross River had been damaged beyond repair.
Initially, local residents installed a temporary crossing, but it was washed away in the first of 15 floods that would impact the area over the next two and a half years. Once the river became unpassable, a 64km drive through back roads was required for even the simplest of trips—including school drop. As a result, many families used kayaks or stand up paddle boards to cross the water to the school bus stop.
InQuik’s solution
InQuik proposed a five-span (13.7m x 4.8m) semi integral bridge, with a full abutment-to-abutment length of 70m.
By raising the bridge level and using a fully integral design, the InQuik® system enhanced flood protection and increased the structure’s overall resilience in the face of heavy loading, flooding, and other natural disasters; even when submerged by the river.
Concrete and steel design would also help to prevent bushfire damage in the future. In addition, the InQuik bridge system meets both T44 and SM1600 design standards, thus meeting the current and future transport needs on behalf of the community.
The Eurobodalla Council installed the InQuik® system using local plant, materials and labour, ensuring funds and work were retained with the local community. Site preparation works included a partial causeway with earthworks, realignment of the bridge for better traffic flow, installation of four piers in the riverbed and headstocks on the piers to support the bridge decks, establishment of abutments on either side of the river.
The installation process was rapid, with bridge span sections positioned in August 2022 and concrete poured later that same month. The concrete was allowed 28 days to fully cure while the approaches and riverbank work was completed. The bridge was ready for service by September 2022.
Then, just one month after being opened, to test the resilience of the structure, the Tuross River flooded. An estimated 120mm of rain fell in just three hours in the ranges just west of Moruya with 170mm in the six hours to 5am. The 2,180km2 catchment area funnelled the rainfall into the Tuross River and the river heights rose to accommodate the flow. At its peak, the water was estimated to be 5m over Murphy’s Bridge.
As the water level receded, the bridge emerged from the river unscathed.
The InQuik bridge is a reliable and cost effective solution, designed to last for a century with minimal to zero maintenance, providing long lasting benefits for generations to come.
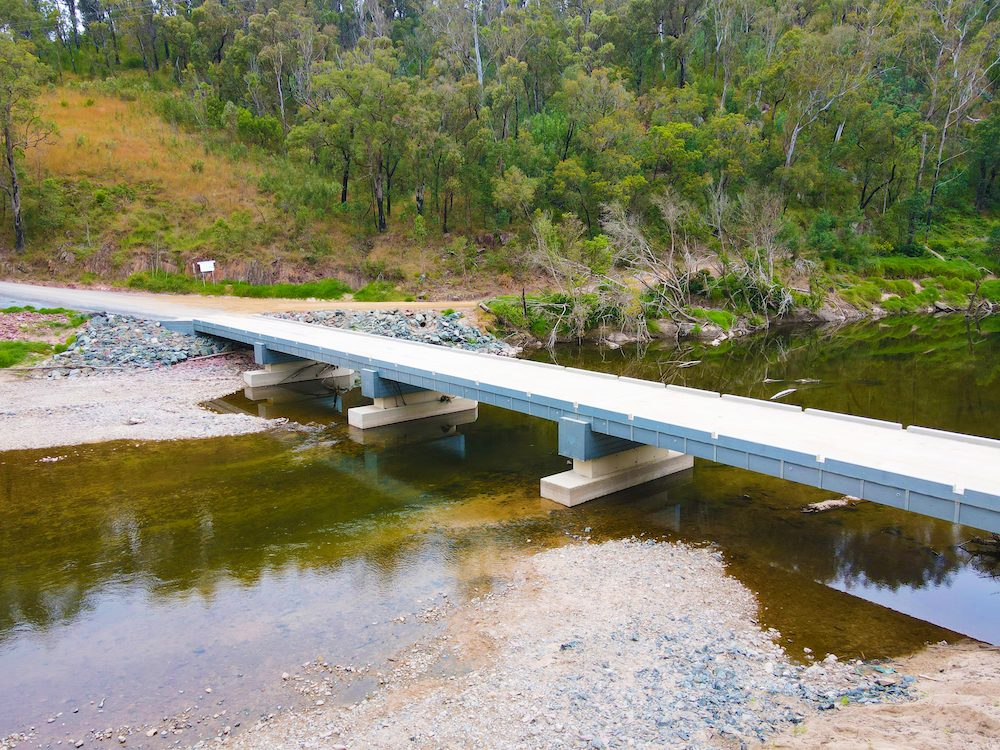
InQuik International Innovation Centre
Construction recently commenced on the InQuik International Innovation Centre (IIIC). The facility, located in Heatherbrae New South Wales, is set to become InQuik’s flagship manufacturing facility in Australia. The facility will not only manufacture product for customers, but also act as InQuik’s innovation hub for new product development, and a training centre for international manufacturers of InQuik products.
According to Michael Wright, InQuik’s director of technology and innovation, “We’ve been working from a rented premises at Tomago since the company was established in 2017. Our rapid growth rate has meant that we’ve outgrown our existing premises. We purchased a block of land 12 months ago and recently started building our own bespoke facility.”
“The entire factory is designed and built for purpose, following our natural work flow—raw material comes in at one end, flows through, and the finished components are shipped out from the other end. The design makes provision for all the cranes and lifting equipment we need, and the size of the bays reflects the width and length of the components we make. Bruce Mullaney our founder, designed the factory and has been very hands-on throughout the construction process.”
“The new facility not only suits what we want now, but what we will need well into the future,” said Wright.
The IIIC was made possible through the support of the New South Wales Government’s Regional Job Creation Fund. The fund supports existing businesses in regional New South Wales to grow, and encourages interstate or overseas businesses to invest in the region. InQuik received a grant of $1 million, and is expected to create 50 new jobs in the Hunter region.