With a rich history spanning 150 years, RUD Australia is a leading provider of specialist solutions for chain technology and materials handling, offering high-quality products and services to diverse sectors such as mining, utilities, engineering and defence. Their in-house capabilities and deep understanding of customer needs enable them to deliver innovative solutions tailored to each project. From their manufacturing and engineering facility in Brisbane, RUD Australia produces a wide range of products, including heavy vehicle hoists, conveyors, and lifting and lashing systems.
RUD Australia provides specialist solutions for materials handling, delivering high-quality products to mining, utilities, engineering, and defence clients throughout Australia and New Zealand. Leveraging broad technical expertise across a wide range of sectors and the company’s one-stop-shop capabilities, the RUD team manage the entire design and fabrication process in-house with.
But what enables RUD to develop innovative solutions is their deep understanding of the customer and their needs – adopting a whole-of-organisation approach to ensuring the best products for their clients.
According to RUD’s managing director, Peter Nuttall, “We understand the customer and their needs. Every company says this, but we actually mean it. We’ve been an innovator and trail blazer for hundreds of years.”
150 years of experience
RUD was established by the Rieger family in Germany back in 1875. It was originally founded as a blacksmith, with a focus on metal chain making. The Rieger family still leads the international RUD Group, which now boasts over 2,000 employees, 500 international patents, and products found in more than 140 countries.
In 1984, Peter Nuttall Senior established the company’s Australian subsidiary, following several years as the local representative of RUD’s tyre protection chain business. Fast forward almost 40 years and with Peter Nuttall (the current managing director), RUD Australia has grown exponentially – with a team of 60 highly-skilled specialists and offices across all major Australian capital cities and New Zealand.
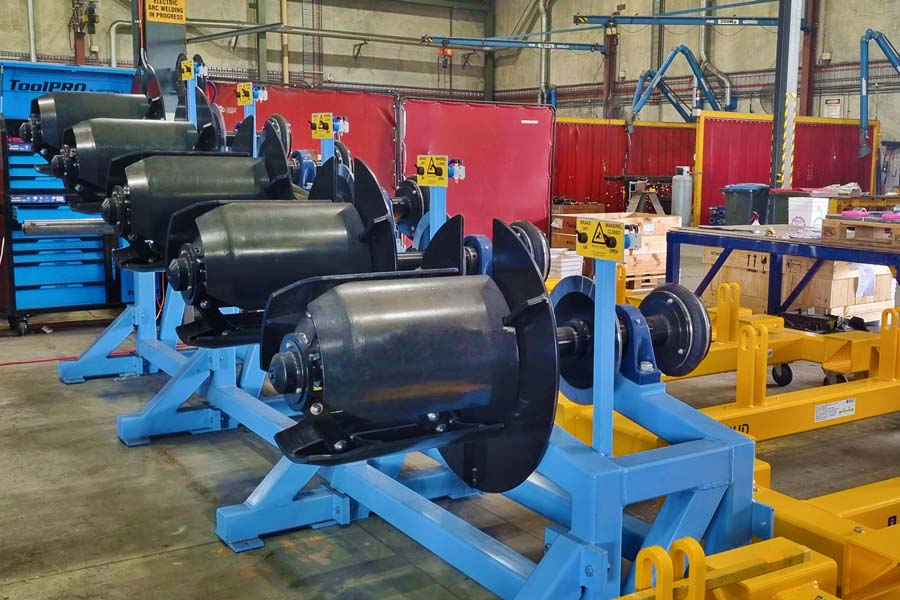
Global solutions made in Australia
Today RUD only has a minor stakeholder share in RUD Australia, giving the local business the freedom to operate fully independently – while harnessing the scale and resources of a global organisation.
“We have all the products that RUD Germany offers: the lifting and lashing products required when using cranes or hoists; conveyors, which are mostly B2B heavy movement of materials haulage in industry like quarries, cement and mining; and tyre protection chains that give tyres a longer life in challenging environments like mines and quarries.”
“We also manufacture Endurequip—Australia’s heavy vehicle and truck hoist system. It is only used by trucks and buses over 7.5 tonnes.”
“To tie everything together, we also offer engineering expertise. So, if someone is building a plant for a particular application, we can design, engineer and manufacture bespoke solutions,” Peter said.
Many of RUD’s products are manufactured locally in RUD’s world-leading manufacturing and engineering facility – a 6,000m2 workshop in Brisbane. RUD has the capability to test fabricated goods and lifting devices in-house, with two 200 tonne test beds and a recently-commissioned 500-tonne test bed. This enables the team to assess their final products, ensuring quality and structural strength that exceed industry standards. With a robotic welder and laser scanning capabilities delivering greater accuracy of design, RUD is able to reverse engineer solutions to suit client specifications. And in addition to market-leading products, the team also offers engineering expertise, designing and manufacturing bespoke solutions tailored to the needs of each project.
Just one of these market-leading products is their five station uncoiler, which is ideal for roll forming companies. The five station uncoiler optimises the use of space around the roll former, helps reduce manual handling and increases safety and efficiency in the workplace. It can be used to perform multiple runs of different colours through the roll former to maximise machine uptime.
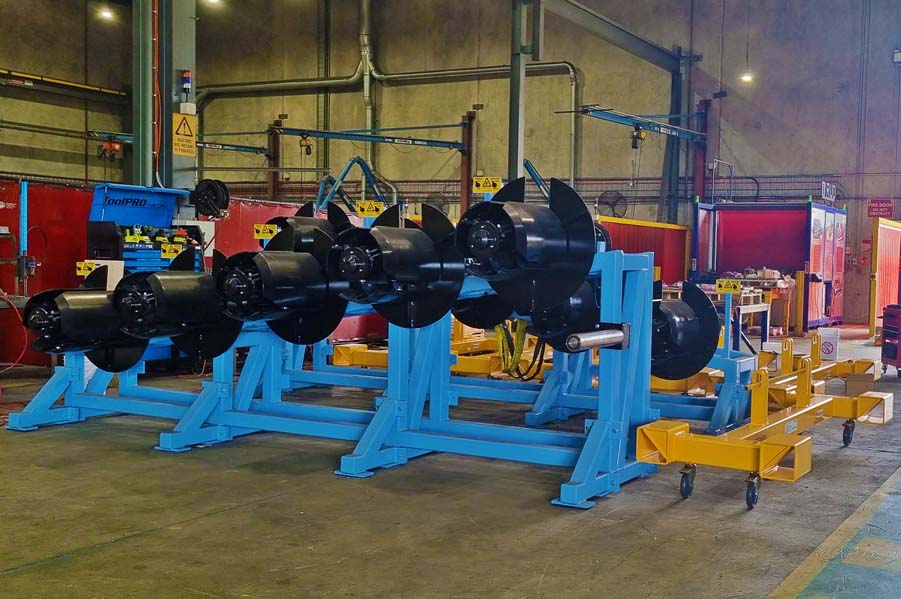
Endrequip heavy vehicle hoists
RUD Australia is the trusted manufacturer of Endurequip heavy vehicle and truck hoist systems, used by trucks and buses over 7.5 tonnes. The Portalift is Endurequip’s highly capable, highly reliable, heavy vehicle hoist, which is suitable for use with a range of different vehicles.
Designed to make heavy vehicle maintenance safe and convenient, the Portalift is the go-to for Australian transport companies, logistics providers, military divisions, and other organisations that need to maintain and service heavy duty vehicles.
The Portalift heavy vehicle and truck hoists use a unique continuous RUD chain drive system that can safely work with weights up to 60 tonnes. This design minimises the need for electrical parts, reducing maintenance costs.
The lifting system provides complete body access, with mobile controls allowing operation away from the lifting zone for increased safety. The system is also water resistant and dustproof, enabling regular cleaning of the fleet without damage. As a robust and portable solution suitable for field deployment, Endurequip is the only vehicle hoist trusted by the Australian Defence Force – and has been used in operations in East Timor and Iraq, as well as across Australia and New Zealand.
To complement the Portalift hoist, RUD Australia also offers vehicle ramps which reduce vehicle turnaround time in the workshop, and a wide range of accessories such as trailer adaptors and vehicle stands.
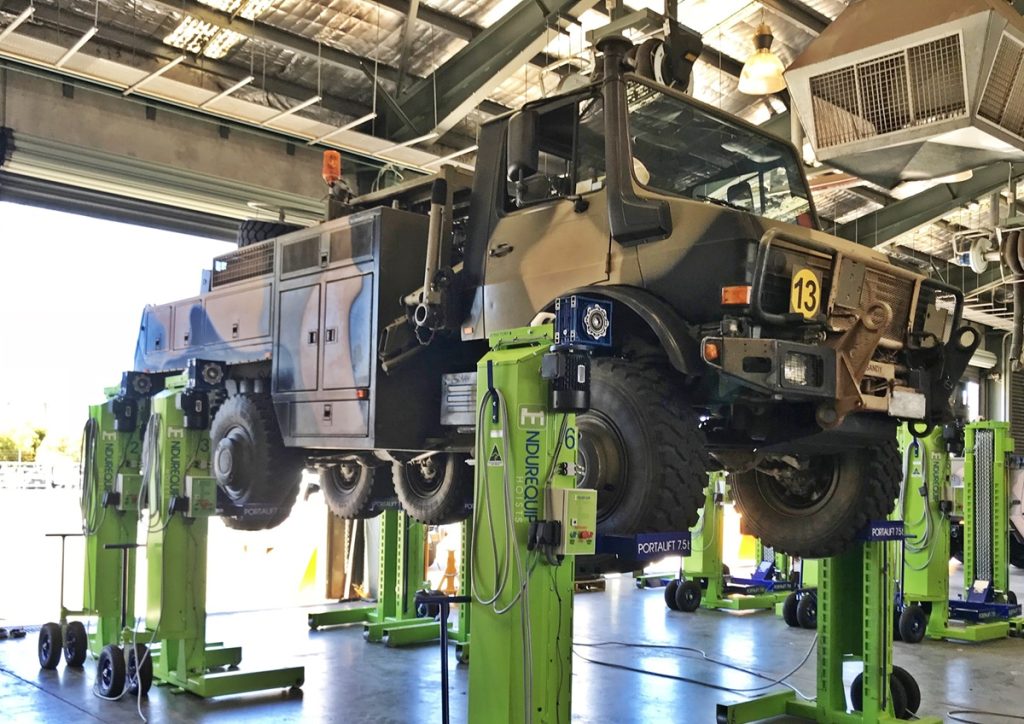
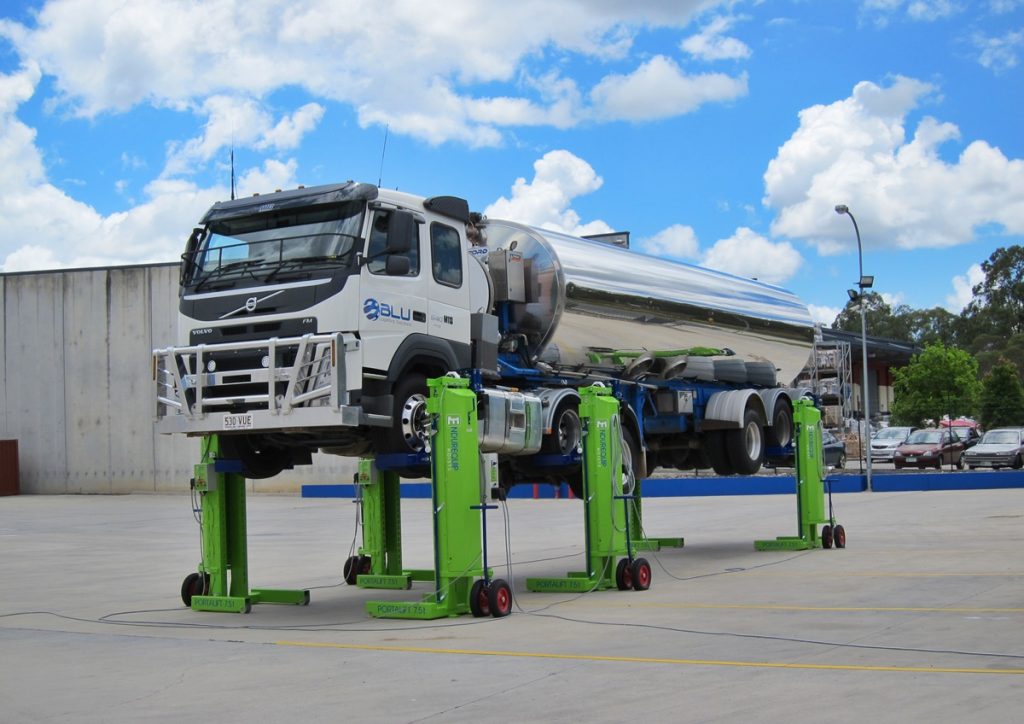
A trusted partner for infrastructure projects
RUD Australia is able to work with clients across a wide range of B2B sectors, including BHP, Wagners, WestConnex in New South Wales, the Australian Defence Force and BlueScope.
“The industries that we serve include mining, quarries, bulk handling, fertiliser, and anything with lifting,
like bridges, girders or lifting
materials inside a workshop or factory,” Peter said.
One major project was the Pacific Highway Upgrade on Exit 41. This project involved the erection of a two span bridge, consisting of seven girders per span for a total of 14 girders, each weighing 85 tonnes.
The crane used in the project was located in the median strip between the northbound and southbound pavements of Pacific Highway, requiring closure of the highway for four nights to ensure safe installation. RUD Australia supplied the hoops and lifting design which was crucial for the safe lifting of the girders.
RUD/Philipp lifting hoops have wire-rope bonded around a concrete core, so they can be used safely for high-load capacities. The hoops can be installed with the needs of recess formers, and connection is simple with a shackle and wire protection pulley or directly to the hook in smaller hoop sizes.
RUD Australia was also engaged in the construction of a new metal recycling plant in Perth, when a high-quality conveyor system was identified as being critical to the plant’s success. Metering and controlled flow were essential features needed in the system, allowing a controlled feed to an inclined belt.
After winning a tender for the design and delivery of the new system, RUD Australia devised a customised apron feeder conveyor system that would ensure continuous, reliable operation to maximise productivity and output.
Operable at various speeds, the conveyor system enabled the transfer of material in horizontal and inclined directions in a single process, with the ability to reverse objects out if needed.
The new conveyor system has proven to be an outstanding solution to ensure productivity in the recycling plant – with a longer lifespan and lower maintenance requirements and costs than the previous system.
And RUD’s role doesn’t end with installation: their dedicated specialists continue to provide ongoing support, delivering and refining the system to ensure the project’s success into the future.
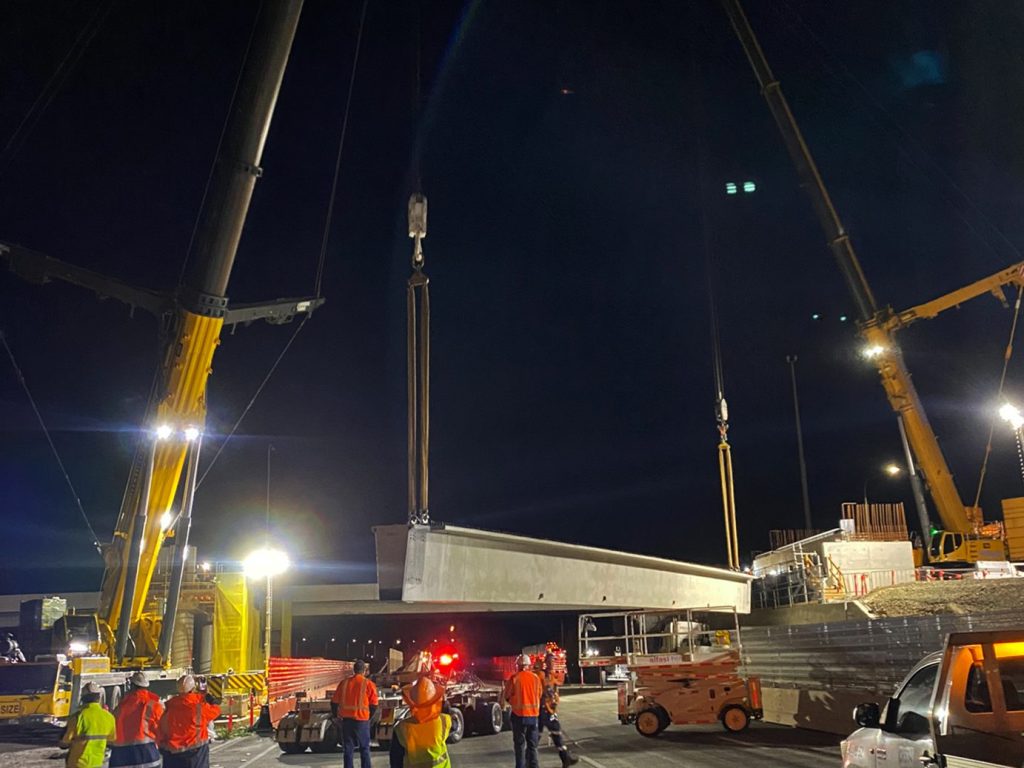
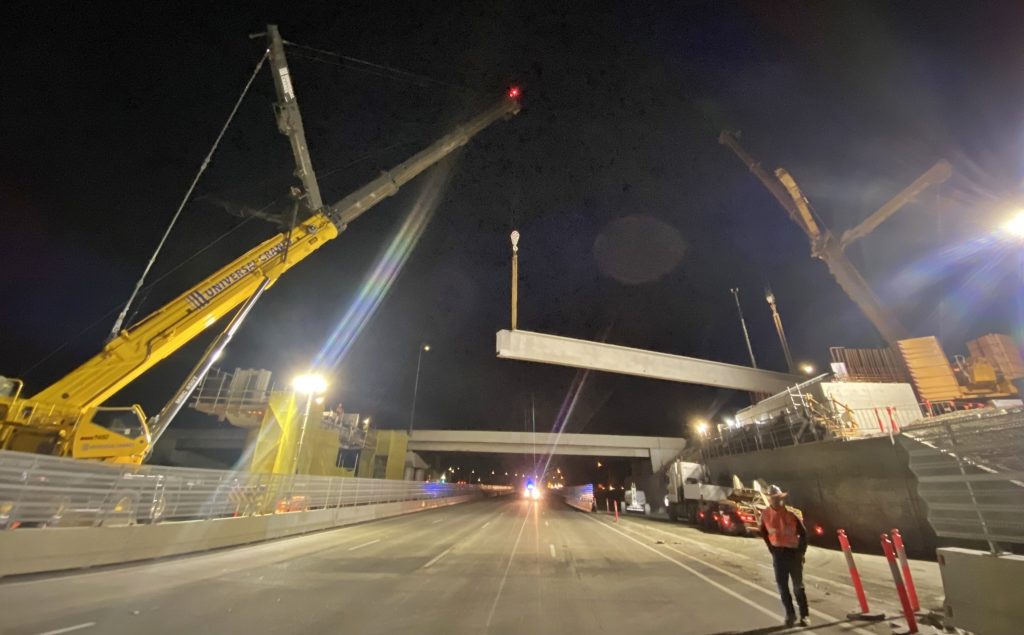
Setting a benchmark for quality
Peter attributes RUD’s success – both locally and globally – to the depth of expertise they have in the products they manufacture and bring to market. The standards set at RUD’s global headquarters in Germany become the standard across much of the world, driving the industry forward as a whole.
“We succeed on the back of the expertise that we have in the products we manufacture and bring to the market. We are experts in the market. We set standards in Germany that become the standard for the entire industry. We were one of the first companies to use grade 80, then grade 100, and then grade 120. Some companies in China are still using grade 80. All our products come from Germany, so they are subject to very stringent quality checking. The expertise and innovation in our products is second to none,” Peter said.
What’s more, RUD has established a reputation as a quality Australian product, with Endurequip hoists manufactured from Australian steel and stamped with the Australian-made logo. Peter added, “People know that when they purchase something from RUD, we’ve used Australian expertise to turn Australian steel into a quality product.”
Project profile: Alfred Street pump lifting solution
RUD recently solved a pump removal problem for Logan City Council’s largest wastewater pump station. The Alfred Street SPS69 wastewater pump station, situated in south-east Queensland, services 200,000 people.
RUD’s engineering team worked closely with the Logan Water and Infrastructure Alliance (LoganWIA), a body established to support Logan City Council’s delivery of water and wastewater infrastructure.
Focused on two key outcomes, RUD developed a lifting solution that: simplified the pump removal process; and ensured maintenance staff no longer needed to venture inside the wet wells, increasing safety.
The challenge
Previously, the SPS69 pumps at Alfred Street were removed for maintenance using two existing bridge cranes (an existing 10 tonne bridge crane and a smaller 2 tonne bridge crane). This configuration was a major issue for Logan City Council’s operations and maintenance staff, as it required personnel to be lowered into the wet well via a ‘man-cage’ using the 2 tonne crane.
LoganWIA understood this method of removal wasn’t a practical or safe long-term maintenance and removal procedure and sought a solution from a lifting and material handling specialists. LoganWIA selected RUD on this project to design and supply a lifting solution that could overcome the existing constraints and hazards.
Upon studying the existing procedures RUD established that:
- The SPS69 pumps weigh 5 tonnes each.
- Each pump sits inside 22m deep wet wells.
- Employees attached 10 tonne crane hooks to the pumps.
When developing the solution for LoganWIA, it was important for RUD engineers to approach a lifting solution with the client in mind. For LoganWIA’s unique access issues, RUD focused on two aims:
- Making the job safer.
- Overcoming the site constraints for efficient removal and servicing.
With these outcomes in mind, RUD identified the following challenges:
- Restricted headroom required a compact design solution.
- This eliminated proprietary systems due to unsuitable lifting bail arrangements.
RUD determined that the station needed new pump lifting points and devices for operating under wastewater and agreed on a comprehensive plan of action with LoganWIA before commencement.
The solution
RUD liaised closely with LoganWIA to devise:
- A 6 tonne WLL lift point for the existing pump.
- A 6 tonne WLL lifting device that would operate when submerged.
- A lifting device with a self-latching hook and a remote hook release mechanism.
- A lifting device that features an axial adjustment mechanism to enable perfectly guided lifting and lowering of the pump. The counter weighted design of the lifting device provides a level lift when the lifting device is empty.
A collaborative approach to safety
With a focus on safety and efficiency, a staged approach to solution testing and commissioning was required prior to the lifting devices being passed for use. This involved comprehensive in-house trial procedures including:
- Testing the device and lifting points to twice the WLL under the AS 4991 2004 requirements.
- Testing the equipment on site to ensure it functioned properly.
- Involving key LoganWIA stakeholders, project partners and others relevant personnel.
The outcomes
The designs for LoganWIA:
- Improved operator safety significantly by eliminating confined space entry requirements.
- Ensured the device retrieves pumps submerged under wastewater, if necessary.
- Proved there is a lifting solution that can be replicated and implemented at other pump stations and deep well situations.
- Offered a compact lifting system for low-headroom scenarios.
RUD liaised closely with all key stakeholders throughout this project to ensure a clear alignment of goals and an in-depth understanding of the safety and maintenance challenges. Then, in collaboration with the client, RUD overcame these challenges.
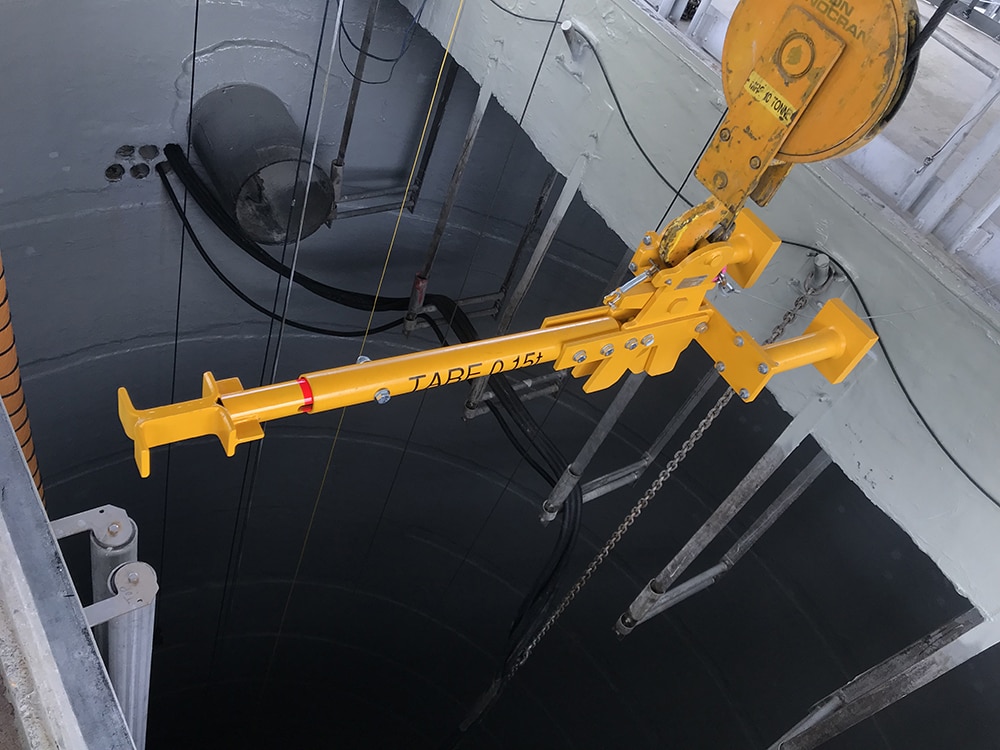
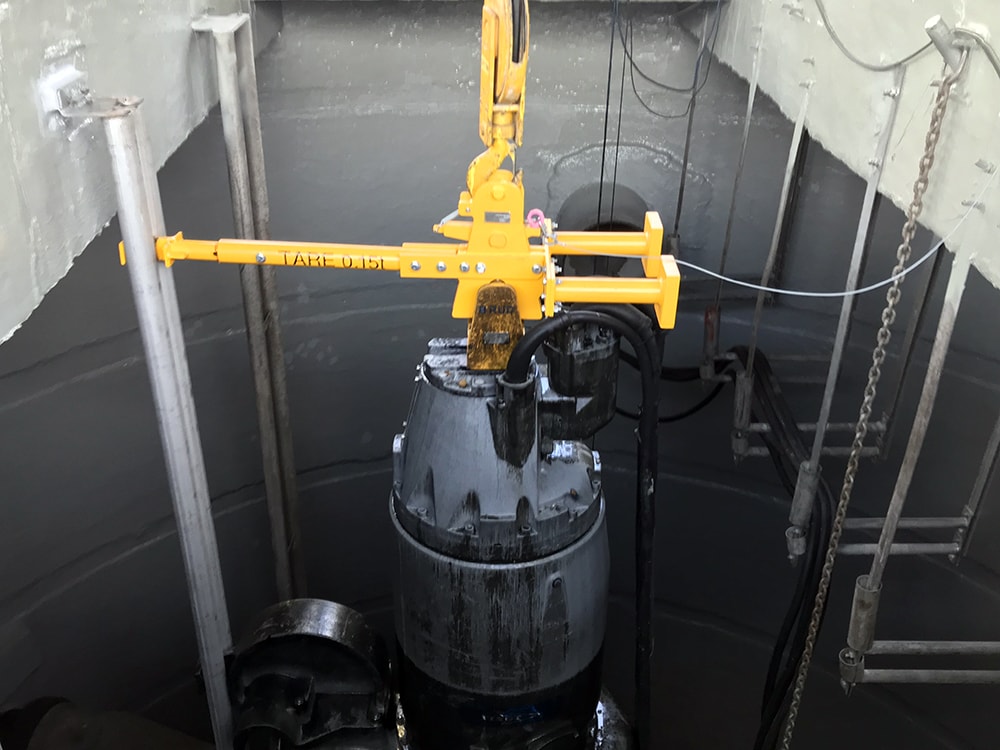