Galserv, a trusted name in galvanizing services to the greater Sydney region, recently marked its 60th anniversary milestone. Since its establishment six decades ago, Galserv has been a stalwart in the galvanizing industry, consistently evolving to stay ahead of the curve. Part of NEPEAN Building & Infrastructure, Galserv has been involved in some of Australia’s largest commercial and industrial projects, helping to extend the durability of bridges, shelters, artworks, road barriers, buildings and industrial-scale precincts—just to name a few.
Galserv began life as Galvanizing Services under the Graham Group in 1963. It was one of the first galvanizers in Australia, and a founding member of the Galvanizers Association of Australia.
In 2007, Graham Group and Galvanizing Services became part of NEPEAN, forming what is now known as NEPEAN Building & Infrastructure, along with leading brands Weldlok and Galintel. Through the decades of continuous improvement, Galserv has always stayed focused on one thing: providing the best possible service to help its client bring the best out in every project.
The Galserv facility in Yagoona is unique, operating 24 hours a day, six days a week, since its inception. Partnered with their process focus, this enables Galserv to handle large and high-volume materials, keeping pace with Sydney’s growing needs. With a demonstrated history of success managing large and complex projects, Galserv’s capabilities allow them to easily handle materials up to 17.5m in length and up to 6.5 tonnes.
What sets Galserv apart is it’s people, many of which have celebrated major service milestones as the business has a strong history of developing and promoting talent. Their team includes an in-house qualified chemical engineer experienced across complex technical projects and provides clients with expert advice and recommendations related to material selection, product design and fabrication for galvanizing to achieve specified quality outcomes.
Members of the Galserv technical team have been trained and qualified to carry out inspections on fabricated steel articles before, during and after the hot-dip galvanizing process. Their team assesses the suitability of articles before the hot-dip galvanizing process including the appropriate use of drainage holes, surface condition, damage and metallurgy and provide recommendations or remedy where necessary.
Committed to making its customers successful, Galserv also provides express services when customers need materials fast.
Future proofing Sydney
Throughout its 60-year history, Galserv has worked across construction and infrastructure projects that helped build an ever expanding Sydney.
According to Joshua Nolan, general manager of Galserv, “There’s been a lot of change in the galvanizing industry since 1963. Every project benefits from our continual improvement across technical knowledge, processing techniques and onsite logistics.”
“These innovations have enabled us to optimise our Yagoona site for large and complex projects – for example, delivering 164 tonnes of hot-dip galvanized steelwork for the world’s steepest passenger railway.”
“Galserv has worked tirelessly to become the trusted leader for even the most demanding steel requirements, including sensitive projects like data centres and military sites.”
“We’re proud of our long history of supporting major infrastructure and construction projects in New South Wales and beyond. We’ve worked on Sydney Harbour Bridge modules, Sydney Boathouse, Taronga Zoo’s elephant enclosure, Sydney Metro stations, Scenic Railway, the Illawarra Fly Walk and almost everything in between.”
“We’re a Sydney business through and through. We’ve been providing pro bono coating services for Sydney’s Heritage Fleet for over 25 years, and previously supported the Westmead Children’s Hospital with project work for their Burns Unit courtyard.”
“Our team at Galserv has worked in partnership for many years with schools and universities across training, research and development to help foster the next generation of talented people. We’re also strong supporters of the galvanizing industry, being a proud founding member of the GAA (Galvanizers Association of Australia) since its inception in 1963.”
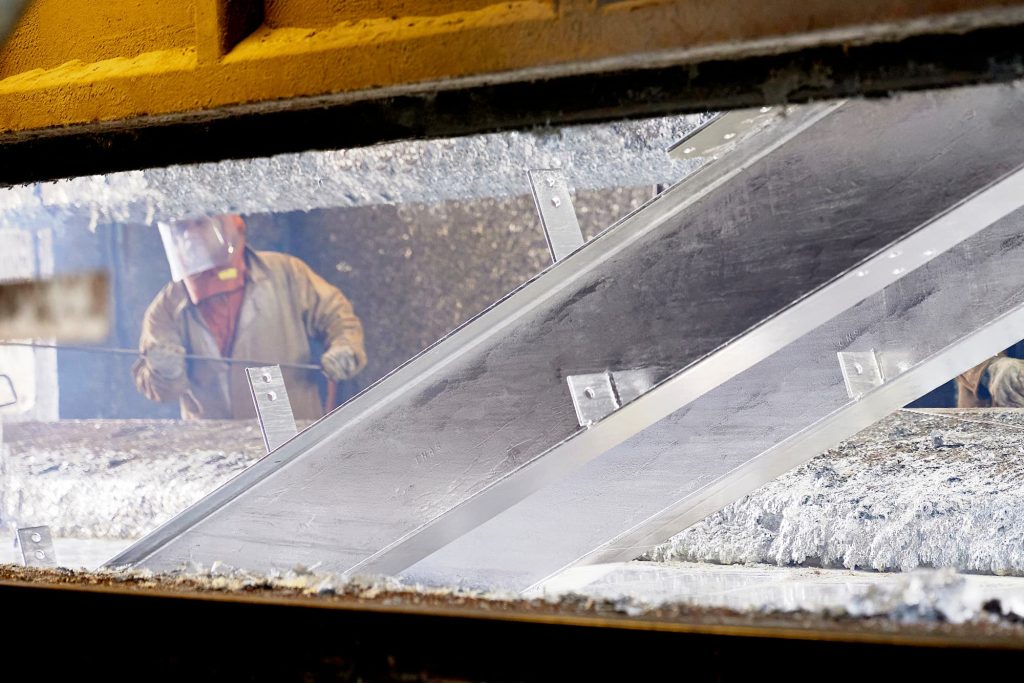
Case study: Katoomba scenic world railway upgrade
The Scenic Railway in Katoomba, New South Wales is the steepest passenger railway in the world. With a 52 degree gradient, the train descends 310m through a cliff-side tunnel, emerging into ancient rainforest at the Jamison Valley floor. Operating since 1945, the Scenic Railway has thrilled 25 million passengers during 700,000 journeys.
The railway was originally constructed in 1880, for a coal and oil shale mining operation, in order to haul the coal and shale from the valley floor to the escarpment above. From 1928 to 1945, it carried coal during the week and passengers on the weekend. The mine was closed in 1945, at which time the railway passed into the Hammon Family hands and has been a privately owned tourist attraction ever since.
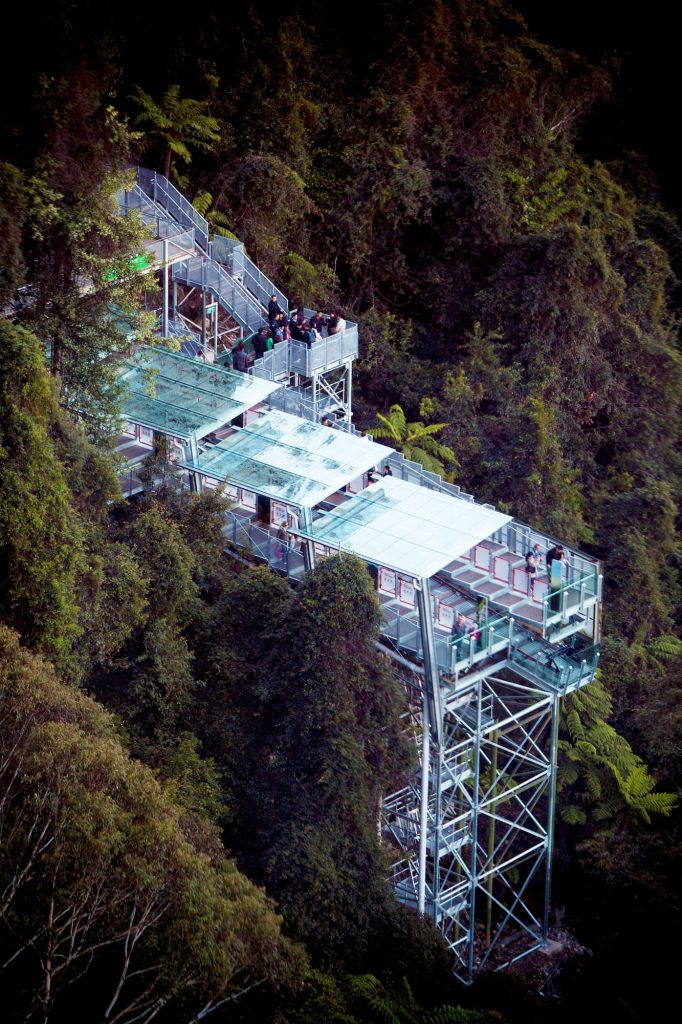
In 2012, Grindley was engaged to undertake a construction management role and to deliver a $20 million upgrade to the railway and associated services. Works included laying of new tracks to accommodate larger Swiss designed railway carriages, upgraded buildings, a new winch and control systems, a complete rebuild of the top and bottom platforms and new restaurant and commercial facilities.
To accommodate the new trains, the tunnel was also enlarged, which involved hand excavation and installation of 140 tonne of mesh reinforced dry shotcrete, with 1.8m, 2.1m and 3.0m long rock bolts.
Combell Steelfab was the prime steel contractor, fabricating 205 tonnes of structural steelwork. The top station, consisting of three levels, service, viewing and queuing platforms and roof steelwork. Main feature columns were painted ‘traffic red’.
Due to the steep site, a series of nine modular tower sections were fabricated for the bottom station including loading and unloading platform steelwork. Because every item was helicoptered into position, the accuracy of their work had to be exemplary. For the Bottom Station Towers, trial assemblies were constructed in Combell’s workshop, and all the project’s structural steel was subject to stringent ongoing quality control.
Galserv treated all the heavy structural material—some 164 tonnes—for the refurbishment, including the support structures for the new upper and lower platforms and all stairways and maintenance access walkways. In total, Galserv galvanized a staggering 17,855 individual steel components. Some of which were installed at an incredible incline of 52 degrees on the track leading into the Jamison Valley.
Galserv worked closely with Combell Steelfab to create an ad hoc delivery plan spanning two months, focused on quick turnarounds for full semi loads of material that were fabricated, galvanized and delivered to site on time.
The figures paint a clear picture of the physical demands of the project:1,100m3 of excavation dug by hand; 240 tonne of existing concrete jackhammered and shovelled out; 143 tonne of existing structural steel cut up and manhandled out; 1,200 tonne of rubbish manhandled out; over 300 micropiles installed to an average depth of 6m and manhandled into position; over 130 tonne of scaffold erected, modified, dismantled and then manhandled up and down the mountain numerous times.
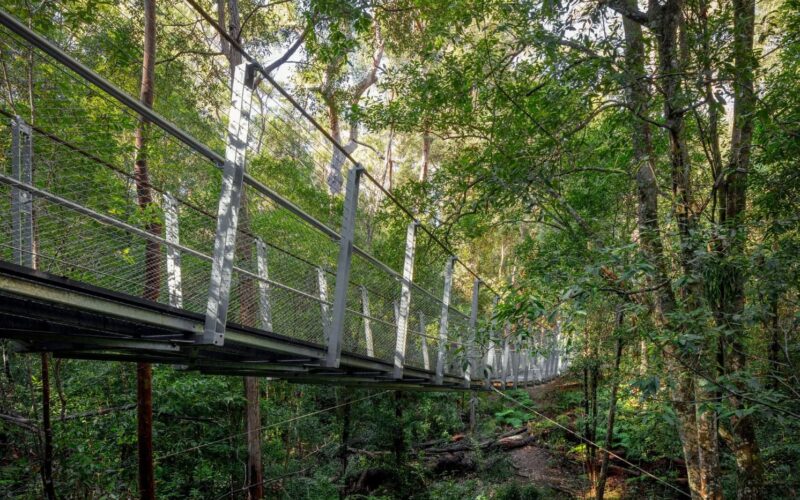
Project case study: Pyes Creek Swing Bridge
The Pyes Creek swing bridge was delivered for Hornsby Shire Council as part of the $250 million New South Wales Public Spaces Legacy Program. Located in a sensitive ecological corridor in northern Sydney, the project brief was to design, manufacture and install a highly functional new pedestrian bridge across Pyes Creek, while causing minimal impact to the surrounding habitat and residents. The solution was a low-profile 50m swing bridge, connecting suburban Cherrybrook with Fallon Drive Reserve in neighbouring Dural.
The single span design was carefully chosen to eliminate the need for cranes and other heavy equipment, while also significantly reducing the bridge’s structural footprint. Featuring 30mm support cables, 32 galvanized steel cross beams and FRP mini-mesh decking, the entire structure was hand-assembled high above the creek before opening to the public in mid-2023.
Working with client Fleetwood Urban, Galserv’s team provided hot dip galvanizing services for 21 tonnes of materials. By utilising innovative design and materials and the longevity of protection provided by Galserv, disruption to the habitat and residents was minimised, providing a long-lasting solution.
This elegant structure enhances accessibility between Cherrybrook and Dural, fostering community connections and a deeper appreciation for our natural backyard. Sustainability was at the forefront, driving every decision, such as using 10m deep rock anchors at each bridge end and eliminating the need for large concrete footings.
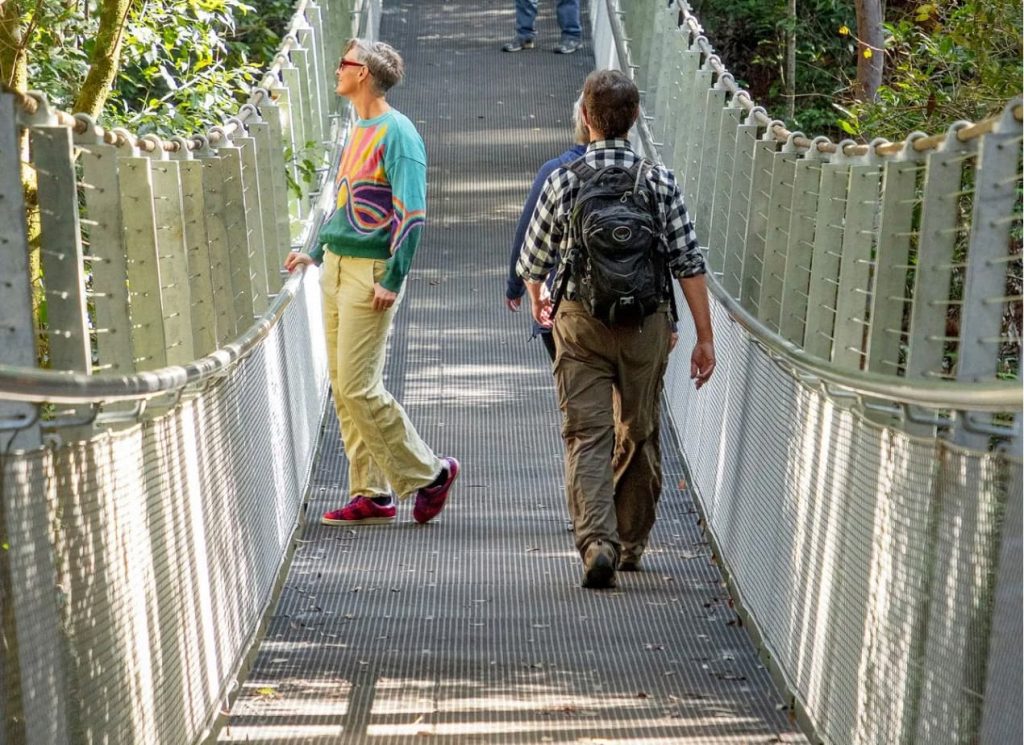