Based in the Riverina in New South Wales, AQUNA Sustainable Murray Cod is an inland aquaculture producer of Murray Cod, the largest freshwater fish found in Australia. AQUNA grows cod in open ponds (or dams) on the Murray-Darling Basin river system—the fish’s native environment.
AQUNA commissioned the Inland Aquaculture Project to help achieve their vision: to make sustainably-farmed Murray cod the fine-dining fish of choice in Australasia and around the globe. The project consisted of the development of 10 round floating aquaculture systems, aeration platforms and winch trusses. In conjunction with steel fabricators, Commins Enterprises, Albury Galvanizing hot dip galvanized all steel sections for the project.
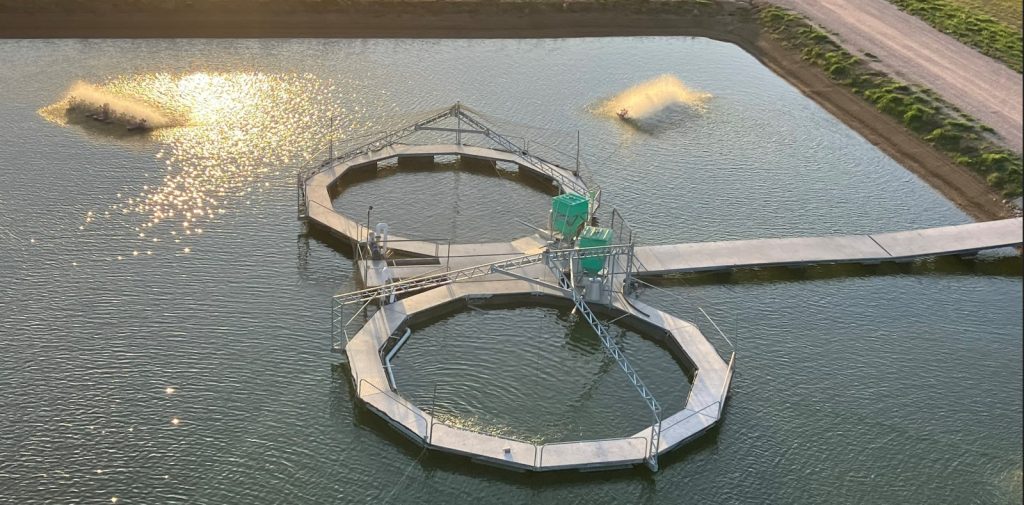
Galvanizing: the best choice
Previously, AQUNA had relied upon rectangular aquaculture systems with either paint coatings or pre-galvanized steel sections.
The choice of hot dip galvanizing for the new design offered a raft of benefits to AQUNA, from improved lifecycle cost and coating durability, through to a major reduction in maintenance. In addition, both construction and erection were much faster as a result of the modular design that galvanizing facilitated.
According to the general manager of Albury Galvanizing Brent Hallows, “Galvanizing was the best choice for the AQUNA Aquaculture Project. Primarily, the biggest benefit was a major reduction in ongoing maintenance for the client. Hot dip galvanizing corrosion protection of all surfaces—inside and out—of the steel sections significantly increased the lifecycle of the asset. The durability of the coating is now a lot stronger, and ongoing maintenance is eliminated.”
Minimising capital expenditure was a critical control point for AQUNA. By choosing galvanizing as the coating system for this project, AQUNA increased the life cycle of the asset three-fold compared to the previous system of pre-galvanized steel and paint.
By extending the life of the asset, AQUNA was able to integrate process improvements into the design itself. These process improvements have dramatically reduced the repetitive manual tasks that were required to operate the system. This has led to both labour efficiency gains and improved health and safety risks.
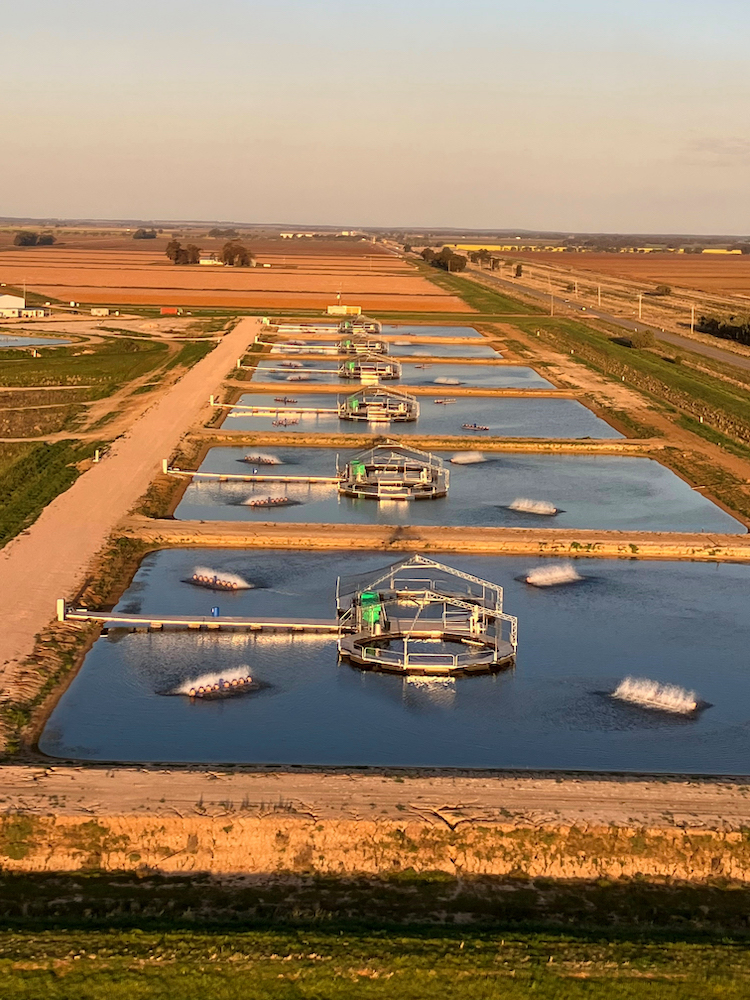
Overcoming design and transport challenges
A project of this scale does not come without its challenges. Due to the size of the modular components, Albury Galvanizing worked closely with Commins Enterprises and AQUNA to refine the design of the segmented platforms.
“The original venting and drainage design meant that the winch trusses could only be dipped in a certain way—there was no flexibility in the process we could use. This would have resulted in needing to double dip the winch trusses,” Hallows said.
“So, we went back to the design with the fabricator and changed all the locations and added venting and drainage holes in the trusses. This allowed us to single dip, which gave a much better overall aesthetic appearance.”
Transport challenges were also encountered due to the size and shape of the components. Albury Galvanizing and Commins Enterprises developed a fabrication and load planning schedule, along with a packaging procedure, that best leveraged maximum use of freight capacity. This reduced overall construction time, as well as the risk of damage during loading and unloading.
“The biggest challenge associated with the project was transport and logistics due to the shapes and quantities of each segment. We had to devise a load plan to maximise the freight capacity and stay on the timeline target. The distance travelled necessitated a load plan that was designed to reduce damage throughout transport and handling,” Hallows said.
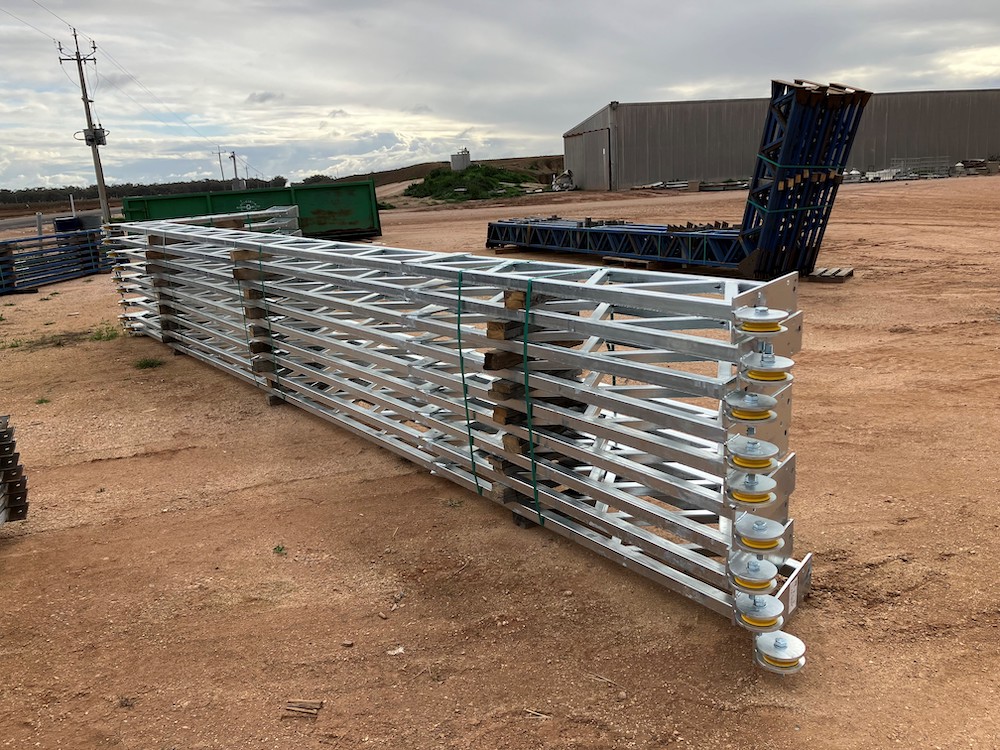
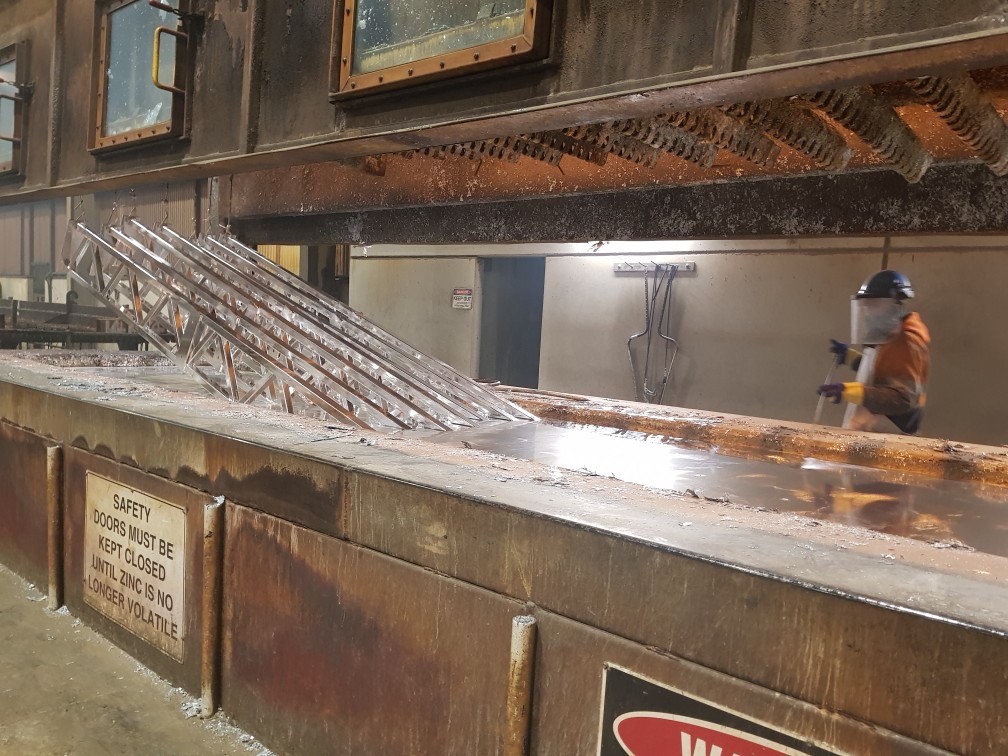
Huge market potential
This world first design for aquaculture systems was only possible through the use of hot dip galvanizing. As such, the project offers almost endless market potential—both locally and globally. With ever expanding global populations and increased environmental awareness, projects such as this are likely to be essential for future food supply and security.
So then, it comes as little surprise that AQUNA is already expanding, with the addition of 12 pondages. “This client is in an expansion phase at the moment. If they reach their expansion target, this would result in AQUNA supplying only 3 per cent of the domestic market—about 0.01 per
So then, it comes as little surprise that AQUNA is already expanding, with the addition of 12 pondages. “This client is in an expansion phase at the moment. If they reach their expansion target, this would result in AQUNA supplying only 3 per cent of the domestic market—about 0.01 per cent of the world market. So the market potential is huge, particularly because it is a sustainable business model and the end product is well-received. There is also additional market potential for further inland agriculture projects,” said Hallows.
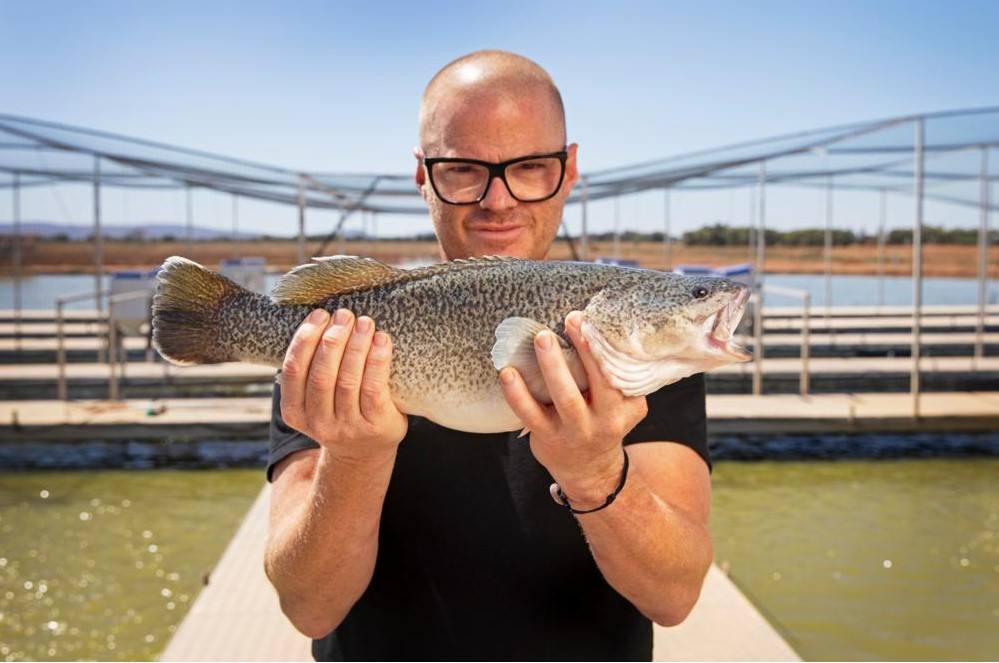
Sustainability in action
Every year, AQUNA sets tangible targets to reduce their environmental impact—they strive to be global leaders in sustainability for the aquaculture industry. With sustainability at the core of AQUNA’s business, hot dip galvanizing was an obvious choice.
“The sustainability benefits in relation to hot dipping galvanizing are linked to the circular economy model. Being galvanized, the design of the system is modular,” said Hallows.
“This means it has a very long life cycle; it can be pulled apart, relocated and reused. It can be pulled apart, regalvanized and then put back into service in 80 to 100 years’ time. Because the asset has been galvanized, it will not need to be replaced every 15 years or so, like other coating systems. It ensures far less maintenance is required,” Hallows said.
“If the client ever decides that they wanted to decommission the project, the steel and zinc can be recycled together to produce new galvanized steel. Galvanized steel can be reused, repurposed, remanufactured or recycled.”
“The project itself also affords a range of sustainability benefits. The aquaculture system utilises 100 per cent recycled water. For example, when the water quality diminishes to a level that necessitates pumping out for the health of the fish, the water is used for crop irrigation.”
“The environmental sustainability benefits and social benefits of a project like this are huge, as is the market potential. To be involved in a project that is so environmentally sustainable, and producing a world class fish product 400km from the nearest ocean, was pretty special,” Hallows said.
Project team
- Client: Murray Cod Australia Limited
- Galvanizer: Albury Galvanizing Pty Ltd
- Steel Fabricator: Commins Enterprises
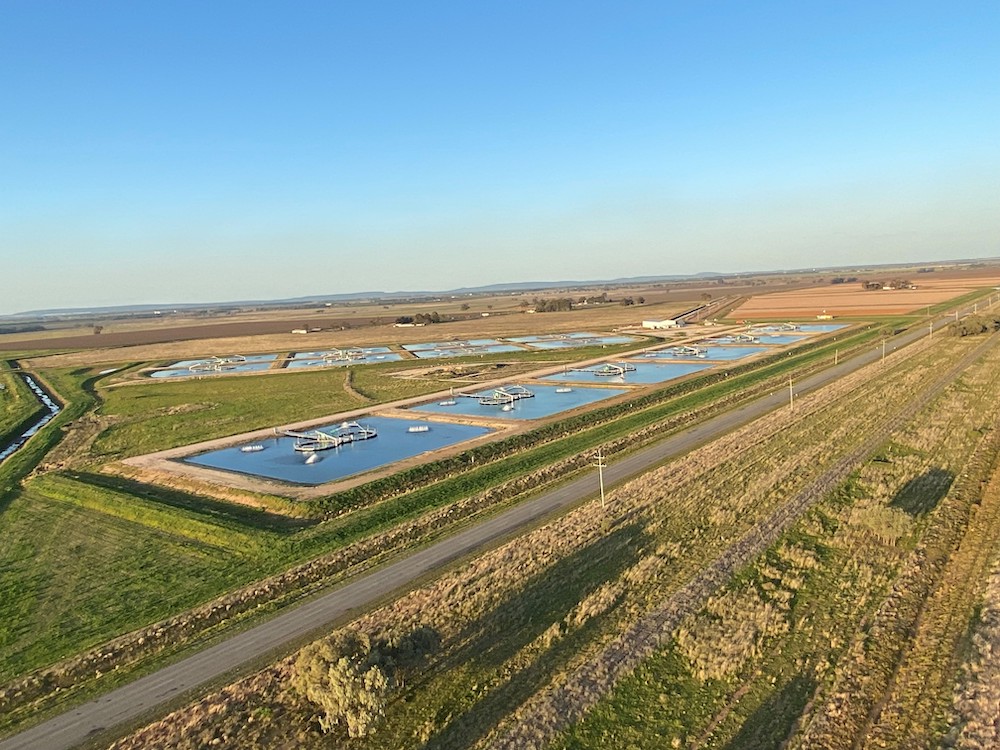